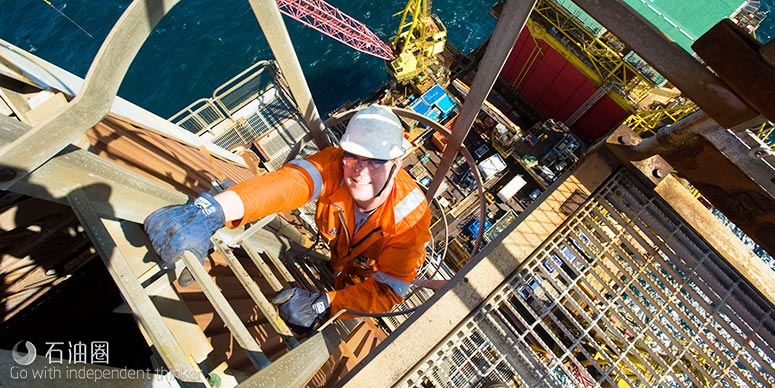
膨脹工具的技術進步,已使其成為了作業公司在整個油氣井生命周期中值得依靠的一項技術。
來自 | TAM International
編譯 | 白小明
膨脹封隔器的主要用途之一是在建井時的固井階段。膨脹元件緊貼在套管上,作為多級固井或井底固井作業的底部支撐,當然這只是膨脹工具最常見的用途之一。在油氣井生產階段要進行修井作業時,如果使用機械橋塞或封隔器存在井下限制,通常需要使用膨脹工具。
例如,可膨脹工具可以采用電纜從生產油管內下入做封堵之用,或者可以與連續油管連用進行過油管擠注作業。通常,過油管作業比較理想;否則,作業公司必須進行壓井以實施油井干預作業。另外,在裸眼完井需要進行油井測試或堵水時,可膨脹工具也非常適用。對于海上油井,膨脹工具也是P&A作業經常需要進行的切割鍛銑工作的理想工具。
套管環空封隔器
套管環空封隔器(CAP)制造加工在標準的API套管上。CAP的組成包括閥套(被固定到在套管壁外)、膨脹元件和滑動端。在膨脹過程中,封隔器的一端滑動以增大外徑。CAP最常用于多級固井或底部固井,在CAP之上連接一個多級固井工具或固井開孔短節,以使水泥返到地面。CAP常用于中間套管,因為井底壓力低,水泥無法返至地面。
這些井段通??焖巽@成,井徑未測量,因此井眼通常沖蝕嚴重。盡管操作人員希望每次都能將封隔器坐封在井徑經過測量的井段,但有時封隔器坐封在沖蝕井段時可能導致膨脹元件過度膨脹,最終破裂。此外,如果環空存在漏失,很難重新獲得套管的完整性,因為套管內徑CAP處的靜液壓力大于環空靜液壓力。閥套用于在破裂的情況下鎖定膨脹元件,通常壓力過平衡情況下不會出現這種情形。雖然經驗表明這是低概率事件,但我們需要針對各種可能性制定解決方案。
為了解決壓力不平衡情況下無法關閉閥門的問題,需要采用新的閥門設計。
新型關閉閥
為此,閥套融入了新技術,以保證冗余性,確保封隔器坐封后,無論環空液位如何,都能保證套管的完整性。該技術正在申請專利,尺寸涵蓋各種套管環空封隔器,已在Permian盆地9-5/8-in井的中間套管進行了現場試驗。無論是在Permian盆地還是其他應用中,通常環空液位較低,或中間套管井段環空存在漏失。
雙級固井作業首先是利用浮鞋進行一級固井作業;投膠塞坐落在浮箍上,打壓,使CAP膨脹。CAP坐封后繼續打壓,將分級固井工具打開;接下來投入開啟塞;然后進行第二級固井作業,水泥泵送完畢后,投關閉塞坐落在分級固井工具上以將其關閉。如果封隔器破裂,啟動新閥門以確保套管完整性。對于此項作業,常規的應急預案通常要等待幾個小時使水泥凝固,然后再打開分級固井工具進行二級固井。
圖4顯示了Permian盆地井的典型井身結構,9-5/8in中間套管下通常是8-1/2in的水平段。CAP的密封元件長10ft,上部接有分級固井工具。按設計膨脹封隔器后,成功實現了二級固井作業。服務提供商的新技術可以確保即使發生小概率的封隔器破裂事件,通過啟動新閥系統仍然可以立刻重新建立套管完整性。

圖4.上圖展示了Permian井表層和中間套管方案,井身結構為9-5/8in套管下為8-1/2in水平段
過油管電纜干預作業
可以使用電纜或鋼絲來坐封膨脹橋塞或封隔器,采用電池供電系統部署和坐封工具,通過馬達/泵總成,采用井下電子元件來控制膨脹過程。作業人員根據坐封井深對作業成功率的重要程度來選擇使用電纜或鋼絲。坐封井深非常重要的情形則采用電纜,因為可以下入伽馬射線和套管節箍定位器,以便在坐封工具之前進行較深。
實際作業中可能需要橋塞或封隔器中的一種。在使用封隔器的情況下,通常使用隔離尾管來隔離井內某一段,近期有一個案例屬于這種情況。一口深水井“A”環空出現壓力變化,監管機構要求作業公司確定位置并進行堵漏。經分析確認是一個隔離封隔器出現泄漏。一種解決方案是動員一部鉆機,起出上部完井工具然后更換隔離封隔器。
但這口井屬于一口低產量(1,500 bpd)的老井,采用昂貴的鉆機修井作業不經濟。因此,作業人員考慮使用電纜系統部署膨脹封隔器的無鉆機作業,如圖5。選擇膨脹技術是因為完井段存在內徑限制,傳統的機械封隔器無法通過。出現泄漏的隔離封隔器位于開孔短節之上。推薦的方案為一次入井在開孔短節之下坐封一個封隔器,然后再坐封一個上部封隔器,上部封隔器下面接著一段無孔管,以便插入到下部封隔器的頂部。這樣就可以將開孔短節隔離,允許流體經無孔管總成流過。

圖5.電纜部署帶膨脹封隔器的BHA的詳細圖
下封隔器坐封后,在其頂部預留有回接筒(PBR),以便上封隔器插入,上封隔器插入PBR后與其鎖定在一起。鎖定機構中的剪切銷允許該總成可以回收。在本案例中,成功坐封了封隔器。無孔管就位后,井筒恢復生產,產量逐漸恢復到之前的1500bpd?!癆”環空未出現壓力變化,滿足了監管機構的要求。此次干預作業的成本僅為鉆機解決方案成本的約5%??蓴U展的補救措施是處于生產后期階段,即產量和壓力已經降低的海上開發井的理想選擇。
您也有讓人撓頭的難題需要解決,或是優質技術想要找應用市場嗎?如果有的話,歡迎聯系小編微信或郵箱,也許能找到一劑良藥。
二丫:131-3255-0596;zhanglingyu@fonchan.com
大安:131-3203-1392;lishian@fonchan.com
For English, Please click here (展開/收縮)
CASING ANNULUS PACKER
A casing annulus packer (CAP) is manufactured onto a joint of standard API casing. The components of a CAP include a valve sleeve (which is fixed to the OD of the casing), the inflation element, and a sliding end. During inflation, one end of the packer slides to allow the OD to increase. The most common CAP application is for secondary cementing or off-bottom cementing, where a stage tool or cementing port collar is placed above the CAP to allow the pumping of cement to the surface. The CAP is often used on intermediate casing strings, when it is not possible to get cement to the surface, due to low bottomhole pressure.
These wellbore sections are typically drilled fast and not calipered, and therefore large wash-outs are common. While every effort is made to place the packer in a gauged section, sometimes the packer is set in a washout, which may result in over-expansion, causing the inflation element to rupture. Furthermore, if the annulus is on losses, regaining casing integrity can be difficult, because there is more hydrostatic pressure at the CAP on the ID of the casing than on the annulus. The valve sleeve is designed to lock-out in the event of a rupture, but an overbalance scenario can prevent this. While experience shows that this is a low-frequency event, the possibility of an occurrence requires a solution.
To address the inability to shut the valve, in the described unbalanced scenario, a new valve design was required to protect against this scenario.
New shut-in valve. To solve the issue, new technology was incorporated into the valve sleeve to provide redundancy, to ensure casing integrity is maintained once the packer is set, no matter the fluid level in the annulus. The technology is patent-pending and available in any size of casing annulus packer. Field trials have been successful in the Permian basin, in wells with 9 5/8-in. intermediate casing. In the Permian basin, and in other applications, it is common to have a low fluid level in the annulus, or for the annulus to be on losses in the intermediate casing section.
The basic operation for a two-stage cement job is to pump the primary cement job through the float shoe. Then, the wiper dart lands on the float collar and pressure is increased to inflate the CAP. After the CAP is set, additional pressure is applied to open a stage tool. Following, an opening plug is dropped. The second stage job is then pumped and a closing plug lands on the stage tool to close it. In the event of a ruptured packer, the new valve sub is activated to ensure casing integrity. The contingency plan at this point is typically to wait a few hours for the cement to setup on the primary job before opening the stage tool to pump the secondary job.
The CAP has a 10 ft seal with a stage tool on top. The packer was inflated as designed and the secondary cement job was successfully pumped. The service provider’s new technology ensures that in the unlikely event of a ruptured packer, casing integrity can be immediately reestablished by activating the new valve system.
THRU-TUBING WIRELINE INTERVENTION
An inflatable bridge plug or packer can be set using wireline or slickline. A battery operated system is used to deploy and set the tool. Downhole electronics are used to control the inflation process through a motor/pump assembly.
Depending on how critical an exact setting depth is to operational success, the operator can use a wireline or a slickline. For applications where the setting depth is critical, wireline is used because it can run a gamma ray and casing collar locator for correlation prior to setting the tool.
A solution may require either a bridge plug configuration or a packer configuration. In the case of a packer, the application is typically to use a scab liner to isolate a section of the wellbore. A recent case history required such an approach. A well in deep water experienced pressure on the “A” annulus and regulators required the operator to locate and repair the leak. It was determined that an isolation packer was leaking. One option would have been to mobilize a rig and pull the upper completion to replace the isolation packer.
But this was an older well producing at low flowrates (1,500 bpd), so an expensive intervention with a rig was considered uneconomical. A rig-less operation therefore was considered using inflatable packers deployed on a wireline system.
Inflatable technology was chosen because a restriction in the completion would not allow conventional mechanical packers to pass. The leaking isolation packer was positioned above a ported sub. The proposed plan was to set a packer below the ported sub on one run, and then set an upper packer equipped with a blank interval of pipe beneath it, to “sting” into the top of the lower packer. This would isolate the ported sub while allowing flow through the scab assembly.
The upper packer assembly was designed to sting into a polished bore receptacle (PBR) that had been left looking up after the lower packer was set. The upper packer assembly was then latched into the PBR. Shear pins in the latching mechanism allowed this assembly to be retrievable. In this case, the packers were set successfully. Once the scab liner was in place, the well was put back on-line and slowly ramped up to the previous 1,500 bpd production rate. No pressure was seen on the “A” annulus meeting the regulator requirements. This intervention was done at approximately 5% of the estimated cost of a rig-based solution. The expandable remedy is ideal for offshore developments that are in the later stages of production, where flow rates and pressures have been reduced.
未經允許,不得轉載本站任何文章: