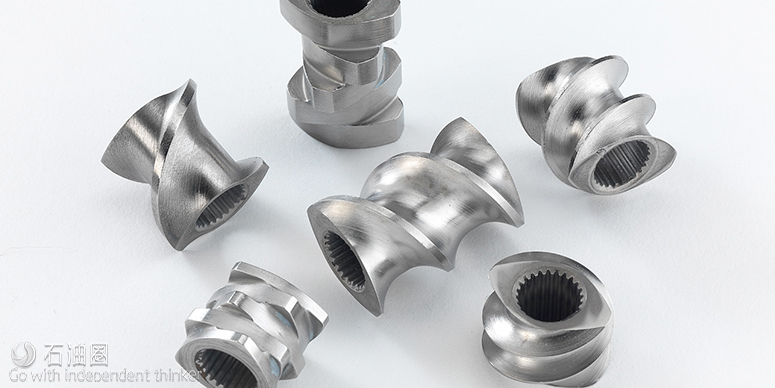
在復雜環境中,如果工具的涂層損壞,那么其完整性將降低!
編譯 | 驚蟄
Hardide公司為新工具提供了涂層方案,通過延長鉆井作業的氣候窗口,每年可為油氣開發商節省數百萬英鎊。井建專業公司DeltaTek Global選擇了Hardide公司的CVD(化學氣相沉積)碳化鎢涂層,作為其ArticuLock新型工具關鍵部件的“盔甲”。
如此一來,ArticuLock就可為作業者提供更長的氣候窗口,從而擁有更充裕的時間來部署海底裝備。同時,還降低了水下送入工具與著陸管柱的彎曲疲勞,提高了作業的可靠性。
Hardide-T CVD碳化鎢涂層可用于工具的關鍵組件,例如復雜形狀的球窩樞軸接頭。在大風、大浪、涌流等惡劣天氣下進行作業時,該組件會承受高達400噸的極限載荷,還可承受5000psi的作業壓力以及30000英尺磅的扭矩。
僅在英國,惡劣天氣造成的鉆井延誤,每年就給作業者造成4億英鎊的損失,高達20%的鉆井預算用于等待天氣。先前無法作業的氣候條件下,作業者利用ArticuLock就可下入工具。它可以將可作業的浪高增加了400%,從1米增加至4米。
樞軸接頭通體由AISI 4330V合金鋼制造,該材質廣泛運用于油氣行業。但惡劣的作業條件意味著該工具需要耐磨涂層。樞軸接頭本體上復雜的溝槽對涂層表面光潔度并不友好,想要實現必要的光潔度還需大費周章。
Hardide涂層公司與DeltaTek公司共同努力,通過單獨的噴涂與拋光,而不是研磨,來達到必要的硬度、厚度以及光滑的表面光潔度。
Deltatek首席執行官Tristam Horn表示:“Articulock將部署于世界上最惡劣的油氣鉆井環境,我們要保證該組件在極端作業條件下也具有最佳性能。樞軸接頭本體的幾何結構復雜,Hardide-T提供了唯一的解決方案。該方案結合了必要的耐磨性,延展性,以及可涂覆性。Hardide涂層公司在上述領域頗有建樹,我們的工具之所以能夠成功為全球油氣作業者提供顯著的成本效益,Hardide涂層功不可沒?!?/span>
ArticuLock在Stena IceMAX上成功進行了現場試驗,這是一種先進的、可用于惡劣環境的冰級鉆井船。預計該工具將應用于北海、墨西哥灣、西非與西澳大利亞等不同地區。
Hardide-T堅固、韌性且耐沖擊的涂層,適用于極端磨蝕與侵蝕的環境,作為低溫CVD(化學氣相沉積)碳化鎢系列涂層,可延長工作在磨蝕性、腐蝕性與化學腐蝕性環境中關鍵金屬部件的壽命。該涂層具有獨特的耐磨、耐腐蝕與耐化學性能,同時還具有堅固、延展性與抗沖擊性。
Hardide-T具有更強的韌性,適用于需要較厚涂層(通常為50微米)的極端磨蝕與腐蝕性環境中的重型應用,或需要抗沖擊載荷的應用。得益于非視線涂敷,該涂層可均勻地涂敷于內表面與復雜的形狀。
由于涂層表面光滑均勻,因此不需要磨削或其他昂貴的精加工作業。其適用于多種金屬,包括各種材質的不銹鋼、工具鋼、合金鋼、鎳合金、鈷合金、銅合金以及鈦合金。
應用領域包括井下工具、閥門、流量控制、泵、密封與軸承表面、重型土方設備、液壓裝置、粉末壓實工具以及模具。所服務的行業包括油氣、航空航天、石化、閥門、泵、材料加工、發電、蒸汽與工業燃氣輪機、工業生產工具、紙漿與紙張加工、食品制造以及賽車運動??蛻艨筛鶕唧w要求訂制涂層。
此外,該技術還可以為許多復雜應用以及其他涂層技術無法解決的磨損、腐蝕或腐蝕問題設計解決方案,例如:Hardide-A專為滿足航空航天工業的需求而開發,因為硬鉻電鍍(HCP)遭遇了歐盟的立法限制,Hardide-A則成為了HCP的直接替代品。Hardide-A與HCP的厚度(100微米)以及硬度(>800Hv)相仿,在幾個關鍵性能方面甚至優于HCP,包括更強的防腐蝕性、耐磨性以及耐化學腐蝕性。而且,在零件尺寸或設計上不需要進行重大更改。
For English, Please click here (展開/收縮)
?
Hardide Coatings has provided a coating solution for a new tool that will save oil and gas operators millions of pounds per year by extending weather windows for drilling operations.
Well construction specialist DeltaTek Global selected the Hardide CVD (chemical vapour deposition) tungsten carbide-based coating for the key component of its new ArticuLock tool. ArticuLock provides operators with longer weather windows to deploy subsea hardware and improve operational reliability by removing bending fatigue in subsea running tools and landing strings.
The Hardide-T chemical vapour deposition (CVD) tungsten carbide-based coating was used on the key component of the tool, a complex shaped ball and socket pivot joint, which is subject to extreme loads of up to 400 tonnes, 5000 psi of working pressure and 30,000 ft.lbs of torque while operating in severe wind, wave and current environments.?
Delays due to bad weather costs operators £400 million per year in the UK alone and up to 20% of drilling budgets are allocated to waiting on weather. Use of ArticuLock will allow operators to run tools in weather environments where previously drilling would have been suspended. It can increase operable wave heights by 400%, from up to 1m to up to 4m.
The severe operating conditions meant that a hard-wearing coating was needed for the pivot joint body which is manufactured in AISI 4330V alloy steel, widely used in the oil and gas sector. The complex grooved geometry on the ball of the pivot joint body presented a further challenge to achieving the necessary post-coat surface finish.
Hardide Coatings and DeltaTek worked together to achieve the necessary hardness, thickness and smooth surface finish through coating and polishing alone, rather than using grinding.?
Tristam Horn, DeltaTek CEO said: “ArticuLock will be deployed in some of the harshest oil and gas drilling environments in the world and we need its components to deliver optimal performance under extreme operating conditions. The geometry of the pivot joint body is complex and Hardide-T provided the only solution that combines the necessary wear properties with ductility and the ability to coat such designs. The Hardide coating delivers in each of these areas and is an important part of the tool’s success in offering significant cost benefits to oil and gas operators worldwide.”
?ArticuLock? was successfully field-trialled on the Stena IceMAX, a state-of-the-art harsh environment, ice-class drillship. The tool is expected to be used in regions as varied as the North Sea, the Gulf of Mexico, West Africa and Western Australia.??
Hardide-T
Tough, ductile and impact resistant coating for use in extremely abrasive and erosive environments
Hardide Coatings
Hardide? is a family of low temperature CVD (chemical vapour deposition) tungsten carbide-based coatings that increase the life of critical metal components operating in abrasive, erosive and chemically aggressive environments. The coatings have a unique combination of abrasion, erosion and chemical resistant properties while being tough, ductile and impact resistant.
Hardide-T
Hardide-T has enhanced toughness and is suitable for heavy duty applications in extremely abrasive and erosive environments where a thicker coating (typically 50 microns) is required or in applications involving shock loads where impact resistance is required.
- Coats internal surfaces and complex shapes uniformly due to non line-ofsight process
- No grinding or other expensive finishing operations required due to smooth and uniform surface ‘as coated’
- Easily applied to a wide range of metals including various grades of stainless steel, tool and alloy steels, nickel, cobalt and copper-based alloys and titanium
- Applications include downhole tools, valves, flow control, pumps, sealing and bearing surfaces, heavy duty earth-moving equipment, hydraulics, powder compaction and tool & die
- Industries served include oil and gas, aerospace, petrochemical, valves, pumps, material processing, power generation, steam and industrial gas turbines, industrial production tooling, pulp and paper processing, food manufacturing and motorsport?
Customer coatings can be developed for specific requirements. The capability of our in-house technical and engineering teams, and the flexibility of our coatings’ properties allows us to develop coatings for your specific needs.
We can engineer a solution for many complex applications and wear, erosion or corrosion problems that other coating technologies cannot solve e.g: Hardide-A was developed specifically to meet the needs of the aerospace industry and as a direct replacement for hard chrome plating (HCP which faces legislative EU restrictions. Hardide-A matches HCP in thickness (100 microns) and hardness (>800 Hv) and outperforms the material in several key properties including enhanced protection against corrosion, wear and chemically aggressive media. No significant changes are necessary in part dimension or drawings.
We recently developed a coating specifically for a customer who needed high chemical purity and enhanced thermal management properties but not coating hardness. The coating was therefore developed with low hardness, high purity and very low internal stresses to meet this customer’s needs.
未經允許,不得轉載本站任何文章: