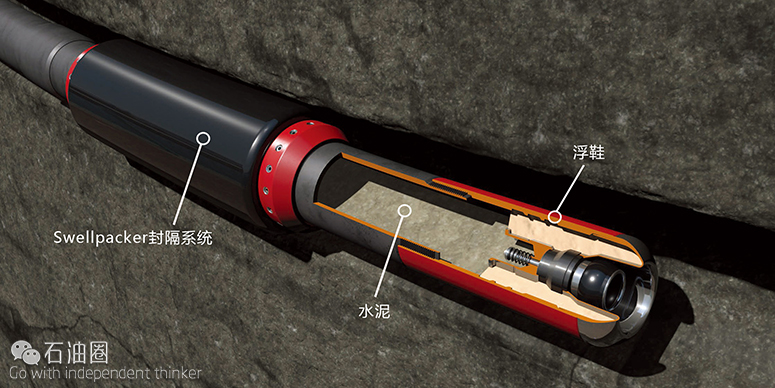
現代油田需要更簡單、更安全、更穩定的井下技術。自膨脹封隔器水平井完井技術式以遇油/遇水自膨脹封隔器作為主要環空風格工具對水平井進行完井的。由于該完井工藝簡單,能夠縮短玩井時間,降低完井風險和費用,已成為油田水平井開發中的一項關鍵技術。
哈里伯頓Swellpacker系列自問世以來,在中東、北海油田已經成功應用上千次。該技術基于特殊橡膠遇水/油膨脹的特性,體積可膨脹至原體積的2倍,從而密封環空周圍,實現有效的層位隔離。部署就位后,該封隔系統可依然保持其膨脹靈活性,適應地層壓力隨時間的變化,進而保持封隔的完整性。石油圈原創www.h29736.cn
同油管結合后,Swellpacker能夠根據基管長度任意調整封隔段長度。另外,Swellpacker具有極高的強度和強大的承壓能力。
Swellpacker封隔系統在套管或裸眼環境中均可使用。在裸眼作業中,運營商可通過使用該封隔系統減少其他相關作業成本,節省鉆進時間并封隔生產層位,這也將油田產能推到了一個前所未有的高度。石油圈原創www.h29736.cn
除上述功能,Swellpacker封隔系統還可用于初次注水泥作業,進一步保證井筒完整性。該系統可提供長期的全面層位隔離,在延長油氣井壽命的同時,還可減少昂貴的潛在修井費用。
延遲膨脹系統
為了確保井筒中的水或油在封隔器下入過程中不會對封隔器造成影響,哈里伯頓設計了多種系統實現推遲膨脹進程,作業者可以根據需求控制膨脹進程,調整坐封時間,減少提前坐封的風險。該系統包括緩膨聚合物以及多種擴散隔膜,獨立或組合使用均可,同時也可根據用戶的井況對系統進行自定義設計。
防擠出擋環設計
除了開發高彈性塑料復合物外,哈里伯頓在膨脹封隔器系統設計中的各個領域都進行著深入研究,如防擠出擋環的設計。防擠出擋環不但能增加封隔器承受的壓差,而且能夠在工具入井時起到引導膨脹的作用。根據應用條件和冶金要求的不同,該設計可以通過定位螺釘、造褶或者焊接來實現錨定。
K2防擠出擋環能夠在封隔器入井時保護橡膠元件,并且在封隔器坐封后防止橡膠被擠出。這種獨特擋環可以在保證承受壓差能力的同時縮短工具長度,可將工具承受的絕對壓差提高到15000psi。
電纜系統
Swellpacker系統能夠通過一個獨特電纜聯通線下入單根或多根控制管線、井下監控管線、化學品注入管線等,且SmartWell完井系統也不用對管線進行切割。如此,整個作業過程無需電纜鉸接、控制管線切割和剝電纜等作業,極大降低了使用電纜的潛在風險。Swellpacker系統不但為套管井和裸眼井提供了環空密封,還賦予了控制管線和數據傳輸管線較強的承壓能力。電纜穿過SwellPacker系統的過程與完井作業同步,全程無需額外的鉆進時間。
系統安裝
安裝Swellpacker系統前需要進行簡單的檢查,然后隨完井管柱或尾管關注下入井中。與此同時即可進行生產,開始膨脹進程,或者將當前流體引入封隔器以引起膨脹,也可直接循環專用膨脹液。Swellpacker系統的安裝無需專門的安裝人員,哈里伯頓提供的工具使得控制管線和扁平管殼在轉盤上的安裝變得毫無壓力。
技術特點
- 可以在任意油田管柱上加工;
- 適用于套管井和裸眼井;
- 結構堅固;石油圈原創www.h29736.cn
- 無移動部件;
- 具有自我修復能力,減少修井次數;
- 可在所有流體環境中使用;石油圈原創www.h29736.cn
- 多種聚合物材料可提供遇油膨脹、遇水膨脹、混合膨脹等特性;
- 膨脹延遲系統。
?技術優勢
- ?安裝時不需要現場專家;
- 維護套管完整性;
- 完美適配不規則井眼形狀;
- 減少作業風險;石油圈原創www.h29736.cn
- 更有效地封隔生產層位;
- 幫助減少油井成本和鉆進時間。
應用范圍
- 裸眼井和套管井;
- 裸眼井和套管井跨隔;
- 監控、化學品注入;
- 出水率控制;
- 獨立篩網防砂;石油圈原創www.h29736.cn
- 劃分篩網/ICD 完井;
- 礫石充填封隔;
- 建井。
應用案例
Swellpacker系列產品目前已在全球多個區塊實現了成功應用。
越南的一個客戶首次決定在一口高溫高壓井的16寸尾管中下入13-5/8”套管并固井。哈里伯頓推測,由于在16”尾管和13-5/8”套管之間存在偏差,這口井將面臨嚴重的漏失問題。此次工程的主要目的是提供一個能夠繼續鉆進的管鞋;從而為新增的層位隔離提供一個二級屏障,防止其被高循環當量密度和管鞋下的低壓區域所影響。
哈里伯頓提出使用Swellpacker封隔系統來幫助提高井筒完整性。由于鉆井作業仍在繼續,作業者要求在6周內工具必須到達井場。而且更具挑戰的是,客戶提出,在入井前對系統進行初步實驗,以證明SwellPacker系統能夠滿足作業者的要求。石油圈原創www.h29736.cn
13-5/8”的Swellpacker系統準時送到,實驗也證明該系統能夠滿足這次作業要求。順利部署入井后,封隔器成功封隔,效果超出了作業者的預期。固井結束10天,Swellpacker工具入井14天后,環空壓力為0且沒有升高。同時,帶有延遲封隔系統的Swellpacker封隔器系統也為初次固井提供了高可靠性的次級封隔。
自膨脹封隔體系在當前油田中有著廣泛的應用。該技術在油田的推廣應用大幅度降低了完井費用,同時也減小了完井事故,提高油井產量,具有重大的現實意義。
小編手中還握有Swellpacker和Halliburton其他產品的更多資料哦,想獲???很簡單:請將此文章分享至朋友圈,發送截圖和郵箱地址至石油圈微信后臺。小編會將資料打包奉上,發送至您的郵箱!還有機會與技術專家溝通交流哦~
來自/Halliburton ?譯者/曾旭洋? 編輯/Leia
Today’s oilfield requires operators to find simpler, safer, and more stable downhole technologies. The Halliburton Easywell Swellpacker isolation system is an innovation that meets all of these criteria. The technology is based on the swelling properties of rubber in hydrocarbons or water, or in both. It swells up to 200%, sealing the annulus around the pipe to achieve effective zonal isolation. Once deployed, the rubber retains its flexibility, allowing the Swellpacker isolation system to adapt to shifts in the formation over time, retaining the integrity of the seal. Its self-healing properties make this a truly innovative technology for all zonal isolation applications. It is a bonded to pipe product that can be delivered with any element length depending on the basepipe length. Since the rubber is bonded to the basepipe, it is extremely robust and can hold significant differential pressures.
The Swellpacker system can be used in cased or openhole environments. In some openhole applications, operators may be able to avoid cementing and perforating altogether, reducing the expense associated with these operations. By reducing well construction costs, saving rig time, and isolating producing zones, the Swellpacker system helps enable previously unachievable levels of oilfield performance.
Cementing Support
For well integrity issues, the Swellpacker isolation system can also be used to complement the primary cement job.The system provides comprehensive long-term zonal isolation, increasing the productive life of the well and minimizing the potential of an expensive workover operation. This combination of proven technologies provides an effective means to address both micro annulus concerns and incomplete cement sheath issues.
Swelling Delay Systems
To ensure that the oil or water contained within the well fluid does not affect the packer while it is run into the hole, Halliburton has engineered several systems that can delay the swelling process. These enable control of the elastomer swelling process as the setting time can be tailored according to the customer’s needs, mitigating the risk of premature setting while optimizing the operating envelope.The systems include polymers with built-in slower swelling properties and a variety of applied diffusion barriers. Customizing a design with either of these options, or using in combination, allows for creation of a well-specific engineered product.
End Ring Design
In addition to the elastomer compound development, Halliburton continues to innovate in all areas of the Swellpacker isolation system design, including the end rings.These important components assist in increasing the differential pressure capability and guide the packer when run into the hole. Depending on the application and metallurgy requirements, the design can be anchored using set screws, a crimping process or welding. In addition, Halliburton has developed a new type of end ring. The K2 end ring protects the rubber element while running in hole and further eliminates element extrusion once the packer is set. One of the benefits of this unique end ring is the ability to shorten the tool length, while maintaining differential pressure. It also increases absolute differential pressure performance of the tools with testing done up to 15,000 psi across the packer.
Swellpacker Cable System
The Swellpacker system can be delivered with a unique cable feed-through option which enables the passage of single or multiple control lines and flat packs for downhole monitoring, chemical injection and SmartWell completion systems without the need to cut the cables or lines. This removes the requirement for cable splices, control line cuts and cable stripping, greatly reducing the risk of failure. It provides an annular seal in cased and open hole, and a seal around the control lines or flat packs capable of holding differential pressure. Installation of the cables through the Swellpacker system is performed on the rig floor at the time of running the completion and requires no extra rig time.
Installation
To install the systems, simply perform standard pre-job checks, then run in hole as part of the reservoir completion string or liner system. At that point either produce the well to begin the swelling process or allow the current well fluid to swell the packer systems prior to operations or circulate down the designed swelling fluid. The simplicity of the operation means that specialized installation personnel are not required. For the cable design, Halliburton provides the installation tool that fits easily on the rotary table and installs the control cable or flatpack through the packer.
Features
- Manufactured on any oilfield tubular;
- Suitable for cased and open holes;
- Robust construction;
- No moving parts;
- Spliceless cable feed-through option;
- Self-healing, interventionless technology;
- Can be run in most all fluid environments;
- Multiple polymers available to provide oil-swelling (OS);
- water-swelling (WS) and hybrid-swelling (HS) solutions;
- Engineered swelling delay system.
Benefits?
- No specialist operator required for installation;
- Casing integrity is maintained;
- Ideal for irregular borehole geometry;
- Alternative solution to cementing and perforating in;
- certain applications;
- Complements cement to resolve well integrity issues;
- Helps reduce operational risk;
- Isolates producing zones more effectively;
- Helps reduce well costs and rig time;
- Cable feature increases system reliability by eliminating cable;
- splicing and enables openhole SmartWell completion systems.
Applications?
- Open and cased hole isolations;
- Stimulation placement;
- Open and cased hole straddles;
- SmartWell completion systems;
- Monitoring and chemical injection;
- Water control;
- Multilaterals;
- Stand-alone screen sand control;
- Compartmentalization for screen/ICD completions;
- Gravel pack isolation;
- Well construction.
Application
?OVERVIEW?
A major operator in Vietnam decided to run and cement a 13 5/8-in casing inside 16-in. liner for the first time in its high pressure/ high temperature (HP/HT) field. Halliburton determined severe fluid losses could be expected due to the very tight annular tolerance between the 13 5/8-in. casing and 16-in. liner. The primary objective was to provide a good shoe to drill ahead and a secondary barrier for added zonal isolation should the cement column be impacted by the high equivalent circulating density (ECD) and the low pressure zone below the casing shoe.
Halliburton proposed using its Swellpacker isolation systems to help ensure well integrity. Since drilling operations were ongoing, the operator needed to have the equipment delivered to the wellsite in only six weeks. Adding to the challenge, a lab test was required to prove that the Swellpacker system design would meet operator internal approval before running it in the well.
The 13 5/8-in. Swellpacker system was delivered on time, and the required lab test report confirming that the packer could be safely run was provided several days before the operation was to begin. The Swellpacker system was then deployed and sealed successfully, exceeding operator expectations.
CHALLENGE
?Reliable secondary barrier zonal isolation in the event of severe losses during the cement job to avoid expensive remedial operations.
- Severe fluid losses anticipated;
- Well control due to huge volume of mud losses to formation and annulus pressure buildup;
- Packer OD of less than 14.65-in. after four days;
- Logistical obstacles to delivering the solution on time.
SOLUTION
Swellpacker systems with delay fusion layer to provide highly reliable secondary barrier to primary cement for zonal isolation.
RESULT
?Swellpacker systems provided effective zonal isolation control along with good shoe to drill ahead provided by cement, saving the operator money and optimizing logistics.
- 13 5/8-in. Swellpacker system was installed trouble-free;
- 10 days after the cement job and 14 days after the Swellpacker system passed the rotary table, the pressure in the C-annulus was at zero and no more pressure had built up.
未經允許,不得轉載本站任何文章: