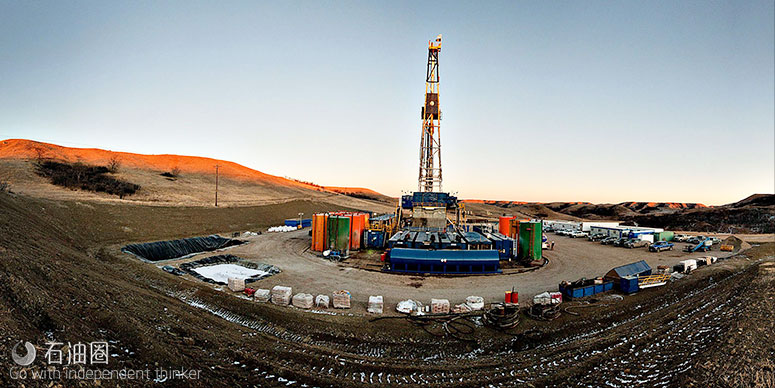
定向井作業經常發生井筒軌跡偏離等問題,技術和觀念的落后是原因。為此,Motive公司拿出了新的方案。
來自 | E&P
編譯 | 張德凱
在非常規油氣藏的開發中,開發商所面對的最棘手問題無疑是鉆井軌跡偏離問題,由于地層條件復雜,實際鉆井軌跡通常會偏離預設的鉆井方案。定向井技術發展的滯后是造成該類問題的主要原因,目前來看,定向井技術已經遠遠落后于水平鉆井中的其他技術。
為了解決該問題,Motive鉆井科技公司研發并推出了新型導向技術,可以在鉆臺操控,實現鉆頭的自動決策導向。
自動決策系統在很多行業中的應用已經非常普遍,包括醫療領域、電子游戲、汽車&飛機自動駕駛、制造業、物流、導彈導航等,而且其應用范圍也正在日益擴大。在過去的五年中,Motive將自動決策系統應用于鉆頭導向系統,并在北美成功地為多家油氣公司進行了水平井、大位移井的鉆井作業,總鉆進長度達610000m。作業結果表明,新型鉆井系統能夠顯著降低鉆井時間、提高鉆進精確度、提高油藏生產潛能,在某些案例中作業人員數量也得到降低。
鉆進提速
在水平井的鉆進過程中,作業專家必須能夠快速做出方案調整決策,在何時轉動鉆桿、在何時改變鉆進方向都是非常重要的。而這些決策的制定也必須建立在大量數據的基礎上,包括鉆頭游動趨勢、馬達狀況、防碰撞導向、狗腿度以及偏離預定軌跡造成的產能變化趨勢等。此外,鉆井專家連續分析的實時數據還包括γ測井數據、大鉤載荷、地面扭矩、泵壓、流率、軌跡測量數據、臨井間距等。
定向鉆井工程師在多年的實際工作中積累了大量的工作經驗,這是他們能及時根據現場數據變化、根據直覺做出決策的依仗。然而,最優秀的定向井工程師不僅要憑經驗、直覺做出決策,還要進行大量的計算,才能得到更優的結果。諾貝爾獎得主Daniel Kahneman在其著作《Thinking Fast and Slow》中寫道:很多時候,人們都太過于依賴直覺。他們在處理問題時,往往會根據直覺做出判斷,而不會進行充分的思考,即使在面對重要決定時也是如此,所以決策結果受人為因素影響極大。定向井作業也是如此,不同作業人員的作業結果總是差別極大。
自動化過程
Motive研發的鉆頭自動導向系統,使用高水平計算機進行大量數據處理,得到的結果更合理,對于定向井鉆井結果有著質的提升。作為提升定向井質量的關鍵部分,該系統不僅能較工程師更快得出結果,還能提供連續的計算數據。此外,該系統還能提供大量、額外的分析和自動化計算,根據動態分析數據、開發商的要求,給予鉆井工程師詳盡、逐步的轉向/鉆進操作指導,大大提高作業效率。
相比于人工計算,計算機的速度和準確率都要更高,這是人工計算無法達到的,因此實時決策的制定更加準確,油藏價值也能得到最優化。該系統的自動計算過程中考慮影響因素非常全面,包括鉆井時間、作業時間延誤風險、油藏生產潛能等;另外,為了降低井筒的摩擦扭矩、提高鉆進速率、最大化水平井觸及范圍、降低水平段漏失、防止產率降低,井筒的彎曲程度也是定向計算中需要考慮的重要因素,而這些在人為計算中往往會被忽略,造成不必要的產能損失。
該系統根據鉆井工程師的作業計劃,連續調整鉆頭鉆進方向,同時給出實時反饋,提高作業效率。由此可見,該系統的自動化達到了前所未有的水平,可持續提高定向井作業人員的工作表現,根據實際數據做出決策,而不是根據經驗、直覺做出調整。
案例研究
下圖所示為Eagle Ford盆地一位開發商采用該系統進行測試的結果。
在此次測試中,該油田使用兩個相同的鉆機,在油藏性質相同的區塊,分別鉆四口井。其中一臺鉆機使用Motive的自動決策工具,另外一臺鉆井則由鉆井工程師掌控。所有的鉆井參數均相同,包括鉆頭、井下鉆具組合、井筒軌跡設計等。
結果表明,采用自動據測工具能夠使鉆井速率提高25%,同時準確率也得以翻倍。

自動決策工具提升鉆進速率25%,提高鉆進準確率2倍
目前來講,該系統還無法做到對井筒的每一項定向井任務進行自動導向,但通過與經驗豐富的鉆井工程師合作,把該系統強大的計算能力與實際作業經驗結合,這將極大提高定向井作業效率、降低作業風險,為油氣開發商帶來最佳作業表現。由于自動決策系統的引入,定向井作業中可能也需要定義新的角色,對變化管理以及新科技接受的程度也將是該系統推廣的關鍵影響因素,雖然有一定的風險,但回報將是豐厚的。自動決策系統除了能夠提高單井的產能和產率以外,還能放大優秀鉆井工程師的作業表現:該系統可以自動進行大量計算,單個鉆井工程師就可同時遠程操控多個定向井鉆井作業的進行。
由于計算和決策制定得到了完美的分工,同時配合自動報告、郵件提醒等功能,整個決策制定團隊(包括作業現場和辦公室內的人員)就能實時掌控井筒的歷史數據、實時計劃調整狀況以及進一步的鉆井計劃,鉆井工程師可同時執行其他任務,作業效率大大提高。該系統能夠將計算結果在可視化界面上進行2D、3D顯示,通過瀏覽器或者移動設備的軟件就能實時觀察。
無論操控人員身在何處,定向鉆井的完全可視化對整個作業團隊都可見,該系統還能將作業結果反饋給開發商,進一步提高鉆井工程師的作業效率。
正如自動決策系統能夠為醫生優化治療方案、使汽車更安全一樣,該技術同樣能提高復雜地層條件下水平井鉆井的效率和連續性。
One of the most significant problems identified by oil and gas operators in unconventional plays is the inability to follow a prescribed well path consistently and to hit and stay within the targets identified collectively by the company’s geologists, geophysicists and engineers. One reason is that directional drilling technology lags behind other technical advances that drove the tremendous growth in horizontal drilling.
To address this problem, Motive Drilling Technologies developed a directional drilling bit guidance system automating decision-making at the rig. Automated decision-making has been used for making medical decisions; for playing games (such as Jeopardy, chess, poker or the ancient game of Go); for automatically piloting cars and planes; for manufacturing, shipping and missile guidance; and for much more. Over the past five years Motive has applied automated decision-making to its bit guidance system’s development and subsequently to the drilling of more than 610,000 m (2 million feet) of horizontal and extended-reach wells for more than a dozen oil and gas companies across North America. Use of the system has resulted in wells drilled with more consistency in less time, with more accuracy and more production potential and, in some cases, with less personnel.
Drilling rates are so fast that even the best directional drillers simply do not have the time to perform all the necessary calculations required to make the absolute best directional drilling decisions. The performance of directional drillers often is quite variable, costing the industry billions of dollars each year due to slower drilling speed, increased tortuosity and lost production potential.
Need for speed
While drilling horizontal wells, directional drilling experts must make quick decisions determining when to rotate the entire drillstring and when to adjust the direction of the drillstring by sliding. These decisions are based upon numerous inputs, including bit walk tendencies, motor yields, anti-collision guidelines, dogleg severity and future production consequences related to deviation from the target path. In real time the directional driller continuously analyzes data including gamma ray logs, hook load, surface torque, pump pressures, flow rates, trajectory measurements, distance to nearby wells and much more.
Good directional drillers rely upon their expertise developed over many years as apprentices to more experienced drillers. This results in an environment where most directional drilling decisions are made quickly based on the individual’s experience and an acquired intuition. However, the best directional drillers also know when they must move beyond intuition and shift to performing more effortful geometrical computations to make good decisions. Nobel Prize-winning author Daniel Kahneman wrote in his book Thinking Fast and Slow that in many situations humans tend to rely upon intuitive thinking too much. They are not willing or do not have the time or energy to switch to more effortful thinking, even when it is required for better decision-making. This unwillingness to adapt behavior contributes to the large variation in performance often seen while drilling horizontal wells.
Automated process
The bit guidance system developed by Motive uses a high-performance computer to provide a more data-driven automated decision-making process, delivering the necessary improvement in directional drilling performance. As a foundation for better decisions, the system automatically performs standard directional drilling calculations previously done by the directional driller but calculates them continuously and faster than humans are able. In addition, the system provides a tremendous amount of additional analysis and automatically provides the driller with step-by-step slide/rotate guidance based on the dynamic analysis together with parameters set by the operator. The machine can run calculations on millions of possibilities/permutations that a human cannot do, thereby making the best decision to maximize value. The automated decision considers such variables as drilling time, lost-time risk and future production potential. Additionally, tortuosity of the wellbore is factored into each directional decision to reduce torque and drag on the wellbore, enable higher drilling rates, extend the maximum reach of laterals and reduce sumps in the lateral that impact production efficiency. This degree of analysis is rarely even considered by human directional drillers.
The system continuously adjusts the guidance based on driller’s actions and provides real-time feedback to enhance his or her performance. This level of automation consistently improves the driller’s ability to maximize value to the operator independent of experience.
Eagle Ford case study
Figure 1 shows the results of a case study designed to test the system for a client drilling in the Eagle Ford Basin. Two identical rigs were mobilized in the same area and drilled four wells each. One rig used Motive’s decision automation tool, and the other rig drilled the wells without decision automation. All other parameters were the same, including bit, bottomhole assembly and well paths. The rig using automation drilled 25% faster and with twice the accuracy.
The system does not completely automate every single task of the directional driller. But the computational power of the system combined with the experience and intuition of the directional driller provides oil and gas operators with the best opportunity for consistent performance at higher levels while mitigating risk. With the introduction of decision automation, new roles might need to be defined, and an emphasis on change management and new technology acceptance is critical. However, the rewards are great. In addition to the gains in performance on an individual well basis, the expertise of the best directional drillers can be scaled. With the system performing all the heavy computational lifting, a single expert directional driller can guide multiple wells from a single location.
With this distributed system, the entire decision-making team (on the rig and in the office) is continuously informed about past, current and dynamically planned future directional drilling activities using automated dynamic reporting, email and text notifications, freeing the directional driller to perform other tasks. The system provides this transparency through 2-D and 3-D visualization interfaces that are available both through a browser and iPad app.
By providing complete directional drilling transparency to the entire team regardless of location, the system returns operational control back to the operator and provides better utilization of the best directional drillers.
Just as decision automation is helping doctors provide better treatments and cars to be safer, this technology has proven to improve the performance and consistency of drilling horizontal wells in today’s tough environment.
未經允許,不得轉載本站任何文章: