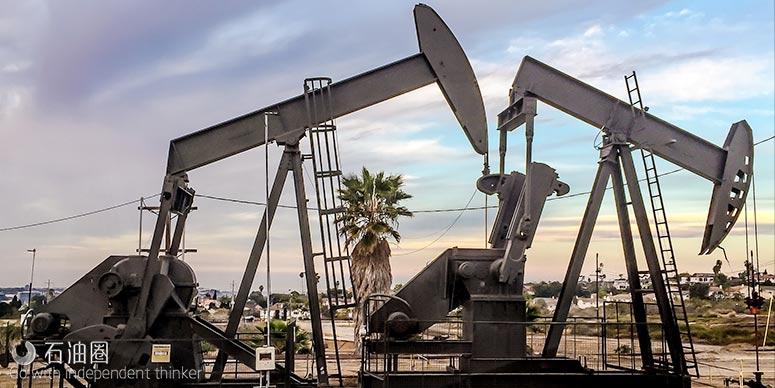
石器時代的結束,并不是因為石頭沒有了,而是技術迭代的結果。
來自 | E&P
編譯 | 張毅
從技術上來講,除了量子物理算是個意外,其他沒有什么是人不能預測的。但在兩年前,當分析人士宣稱,頁巖油氣行業將無法在油價低于60刀的狀況下維持生計時,卻很少有“算命大師”能看到這個行業的前景究竟如何,也就更少有人能預測到如今頁巖油氣生產的爆發式生長了。
事實上,有很多指標能精準地判斷出石油市場會在何時陷入谷底。大部分數據顯示,油氣市場在2016年1月觸底,當時西德克薩斯的半成品油價格跌至$29/bbl;而到5月底,美國的工作鉆機數量就已經降至僅剩404臺。而時隔兩年以后,行業內卻出現了戲劇般的爆發,美國已成為凈石油生產國,鉆機數量現已恢復至2015年的水平。
在這背后,“技術”的戲份可以說是最多的。
防砂系統能夠在高流速下保持效率

ENERGES出砂管理服務將傳統技術與新型技術相結合,可提供不同需求的除砂選擇。ENERGES采用雙旋風除砂分離器,該分離器內設二級固相分離裝置,能夠使更多的細砂 “脫落”,同時也高效解決了翻塔的問題,也就確保了下游設備的無砂。ENERGES在用戶現場進行了多個測試,評估出砂管理系統的有效性,兩個雙旋風除砂分離器都用于處理100目的返砂。其中,第二個除砂分離器下游安裝的聲波監測傳感器記錄到,有10%~25%的砂翻塔進入下游流程。
在安裝除砂過濾器后,過濾器下游檢測出的砂量為0。通過檢查生產分離器,該數據得到了確認。除了除砂之外,ENERGES還可在除砂率保持在100%的前提下,使用更大尺寸的油嘴。這種改變說明,該過濾器能夠在高流速下維持較高的除砂效率。上述技術可保護生產設備免受出砂損壞,同時也可減少頻繁關井的問題,保障連續生產。
軟件通過實時數據提升壓縮機性能

Flogistix LP公司是一家壓縮機制造商,同時也為陸上油氣作業提供油井優化服務。該公司推出Flux系統,可為壓縮機單元提供實時數據,提高用戶的設備運行透明度。除此之外,Flux系統還可識別長期趨勢,克服業內最大的生產挑戰—停產。通過實時遙測、運行參數和檢修記錄證明,Flogistix公司憑借Flux系統可保證設備有效運行時間長達98%。系統捕獲壓縮機的工況變化,并將這些變化體現在時間軸上,與其他關鍵傳感器數據進行對比,旨在為用戶提供整體畫面和更加深入的信息。Flux系統的實時數據采集和長期趨勢預測的能力,使其成為了優化生產的有效工具。
柱塞舉升系統用于非常規油氣井增產

Flowco公司近期推出了自動化柱塞氣舉系統,該系統將現有人工舉升技術、高級自動化軟件運算法則和監測技術相結合,目前已在全球范圍內的多口水平非常規油氣井實現了降本增效。值得一提的是,融合氣舉和柱塞舉升系統省去了成本高昂的修井作業,在油井和氣井的合采應用上都能實現長期利益,而北美運營商正品嘗著這塊美味蛋糕。柱塞協助氣舉系統,再搭配自動化應用,目前已經達到了降本的效果,同時也延長了水平非常規油氣井的生產周期。
上述舉升系統改善了頁巖井產量快速衰減的問題,也讓作業者得以應對高氣水比和高出砂/固相的井,效果顯著優于其他舉升設備。
新型隔離工具為高壓工況設備提供保護

現代水平鉆井和多級壓裂,給油氣設備帶來了前所未有的嚴苛工況。在此類完井作業中,地面井口設備需要得到有效保護,來對抗高壓、高流量工況。
Greene能源集團推薦使用隔離工具,保護井口設備免受高壓和粗糙原料的沖擊,同時也能保護作業人員免受意外壓力泄放造成的傷害。Greene公司的Guardian井口保護工具可協助作業人員通過現有井口直接進行壓裂作業,免去了壓井作業,同時也降低了除砂與沖蝕的概率。
現有三種的工具Tree Saver、Casing Saver、Stage分別用于油管、套管與井口的封隔,都是利用液壓缸/液壓單螺桿將工具的主心軸通過井口插入實現的封。三者的平均安裝或拆除時間為30分鐘,同時井口保護技術的使用能夠免除傳統租用壓裂井口成本高昂的修復工作。
新型服務系統用于識別管線損壞

哈里伯頓推出的聲波測量(ACX)和電磁管線測量(EPX V)服務,可協助作業者快速識別泄漏位置,并描述出需要修補的管線破損程度。
流體成像工具ACX能夠將管線后部流動進行定位并成像,主要用于流動保障,油氣井完整性與井漏識別。該工具能夠映射包括環空之間的井眼附近流體的流動,并貫穿于整個完井作業過程。
井漏成本昂貴,針對這一問題,主要需進行漏點定位和漏點修復兩個環節。對于鎖定泄漏位置環節,有常用的幾個操作方法,但過程往往耗時很長,且效果差強人意。當存在腐蝕問題時,EPX V管線檢測工具可利用精確高頻HD技術,對井眼內1~5個同心管柱的金屬損失進行量化。該工具只需單次下入,就可協助用戶對整口井進行檢測,并評價管線情況。EPX V通過向周圍管線引入高清頻率電磁能,可在沒有井眼流體的影響下,通過同心管柱進行擴散;隨后信號返回給工具,最終生成反映每根管柱金屬損失的有效信息。
您也有讓人撓頭的難題需要解決,或是優質技術想要找應用市場嗎?如果有的話,歡迎聯系小編微信或郵箱,也許能找到一劑良藥。
檸檬:186-2292-2332;weiyameng@fonchan.com
二丫:131-3255-0596;zhanglingyu@fonchan.com
For English, Please click here (展開/收縮)
SAND MANAGEMENT SYSTEM HANDLES HIGH FLOW RATES, MAINTAINS EFFICIENCIES
ENERGES Sand Management uses traditional and emerging technologies to provide a full range of de-sanding options. ENERGES uses dual cyclonic sand separators with engineered inserts for second-stage solids separation to create additional fine sand “fall out,” and the sand filter effectively eliminates the carryover to deliver solids-free production. Several tests were conducted on customer sites to measure the effectiveness of the sand management system. Two dual-cyclonic sand separators were used to combat the 100-mesh sand returns. Acoustic monitoring sensors downstream of the second sand separator were registering that 10% to 25% of entering sand was still carrying over. After installation of the sand filter, sand production downstream of the filter registered zero and was confirmed by checking the production separator. In addition to the successful removal of fine sands, choke sizes were increased while maintaining 100% sand removal. This ramp-up in production shows the filter’s ability to handle high flow rates while maintaining de-sanding efficiency. These technologies mitigate production equipment damage from sand and reduce frequent well shut-ins for maintenance, keeping production online.
SOFTWARE ENHANCES WELL COMPRESSION WITH REAL-TIME DATA
Flogistix LP, a gas compressor manufacturer and well optimization service provider to the domestic onshore oil and gas industry, has released its newest software, Flux. Flux provides real-time insight into compressor unit performance and gives companies enhanced transparency. The system also offers the ability to identify longterm trends, ultimately reducing one of the industry’s main production challenges: downtime. With Flux, Flogistix guarantees a run time of 98%, proven through real-time telemetry, run-time statistics and maintenance history. This is accomplished by capturing changes in the state of a compressor and representing these events on a time line with other vital sensor data, providing context and insight to the user. The ability of Flux to capture real-time data and long-term trending makes it a tool for optimization.
PLUNGER LIFT SYSTEM IMPROVES PRODUCTION FOR UNCONVENTIONAL WELLS
Flowco Production Solutions has recently released its plunger lift-assisted gas lift with automation. This new application of existing artificial lift techniques along with advanced automation software algorithms and monitoring has helped reduce operating costs and improve the production of horizontal unconventional oil and gas wells throughout the world. Specifically, North American E&P operators are experiencing huge benefits of commingling gas lift and plunger lift without the high workover costs of any select pump apparatus—considering that gas-lift and plunger lift systems are the only two artificial lift systems that marry well together with long-term benefits in both oil and gas wells. The application of plunger lift-assisted gas lift coupled with automation has allowed the industry to reduce operating costs and extend the life of rapidly declining horizontal unconventional oil and gas wells. This new artificial lift has improved the way a gas-lift installation operates in the life cycle of a rapidly declining shale well. It also allows the operator to maintain the ability to handle high gas-liquid ratios and sand/solids from the well with no problems, unlike other forms of artificial lift. The system is designed to prolong the need for artificial lift conversion to positive displacement pump and reduce the operator’s monthly well costs by optimizing compression. Horizontal wells are not an issue for plunger lift or gas-lift systems as experienced with positive displacement pumps. The deep lift opportunity of Flowco’s applications helps increase profit margins on product sold by reducing operating costs, reducing workover costs for repair and maintenance and increasing production.
ISOLATION TOOLS RECOMMENDED FOR PROTECTING EQUIPMENT AMID HIGH PRESSURE
Never before has oil and gas equipment been subject to such abrasive conditions as found in modern horizontal drilling and multistage fracturing jobs. During these challenging completion operations, surface wellhead equipment needs to be efficiently protected from high-pressure, high-volume conditions. Greene’s Energy Group recommends the application of isolation tools to protect the wellhead equipment from high pressures and abrasive materials as well as protecting personnel operating at surface from unplanned pressure events. Greene’s Guardian Wellhead Protection tools allow operators to fracture directly through the existing wellheads, eliminating the need to kill the well and reducing the possibility of sand and erosion, which causes valves to fail during the operation. There are three different versions of the tool system that seal off in tubing, casing or the wellhead. The Tree Savers use hydraulic cylinders to insert the main mandrel of the tool through the tree and wellhead bore and sealoff in the tubing inside diameter (ID). The Casing Savers use hydraulic cylinders to insert the main mandrel through the tree, wellhead bore and seal-off in the casing ID. The Stage Tools use a hydraulic single screw to insert the main mandrel through the tree and seal-off in the wellhead bore. The average installation or removal time is 30 minutes, and the use of wellhead protection technology can eliminate costly repairs to conventional rental fracturing trees.
SERVICE SYSTEMS HELP FIND PIPE DAMAGES, OFFER EFFICIENT SOLUTIONS
Halliburton provides time-saving analysis through new technologies. Accurate diagnostics are critical to help keep projects on budget and on time. The Acoustic Conformance Xaminer (ACX) and Electromagnetic Pipe XaminerV (EPX V) services help operators quickly find a leak’s location and describe the extent of the damaged pipe that needs fixing. Halliburton created the flow imaging tool ACX, which locates and images flows behind pipe(s) and is primarily used for flow assurance, well integrity and well leaks. The tool can map fluid flow around the wellbore, including in between annuli and throughout the completion. Well leaks are very costly to production returns, including the cost of locating and repairing them. There are several operational techniques for narrowing down a leak’s location. However, these can be time-consuming and might not fully explain what is occurring. When corrosion is a problem, the EPX V pipe inspection tool quantifies metal loss in one to five concentric strings of pipe in a wellbore using accurate high-definition (HD) frequency technology. The tool helps customers examine the whole well in one trip and assess pipe condition. The EPX V operates by inducing HD frequency electromagnetic energy into the surrounding pipe, which propagates through the concentric well strings with no wellbore fluid influences. The interaction with the metal of the pipe returns signals to the tool, yielding information about the state of metal loss in each pipe.
未經允許,不得轉載本站任何文章: