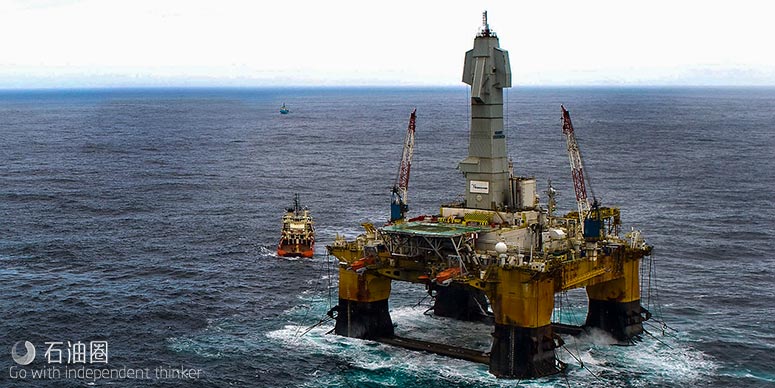
膨脹工具的技術進步,已使其成為了作業公司在整個油氣井生命周期中值得依靠的一項技術。
來自 | TAM International
編譯 | 白小明
膨脹封隔器的主要用途之一是在建井時的固井階段。膨脹元件緊貼在套管上,作為多級固井或井底固井作業的底部支撐,當然這只是膨脹工具最常見的用途之一。在油氣井生產階段要進行修井作業時,如果使用機械橋塞或封隔器存在井下限制,通常需要使用膨脹工具。例如,可膨脹工具可以采用電纜從生產油管內下入做封堵之用,或者可以與連續油管連用進行過油管擠注作業。通常,過油管作業比較理想;否則,作業公司必須進行壓井以實施油井干預作業。另外,在裸眼完井需要進行油井測試或堵水時,可膨脹工具也非常適用。對于海上油井,膨脹工具也是P&A作業經常需要進行的切割鍛銑工作的理想工具。
測量裸眼原始應力
明確裸眼井段的原始應力有諸多益處,首先,地層應力對于注水井非常重要,因為需要知道油氣藏蓋層的巖石強度以確保注入區的壓力完整性,并且要確保不形成可能使注入流體竄到區域以外的裂縫。原始應力數據還可幫助工程師選擇最佳的套管下入深度。鉆井團隊在設計套管鞋深度時,當井下信息受限或者采用預測模型時,他們通常比較保守。如果套管下太早可能會增加成本;而如果下太晚,可能過于激進,導致井控問題,甚至要啟動成本高昂的應急預案。
常規測量原始應力的方法是采用電纜部署的地層測試工具。然而在井斜大于30°的井中,可用的液壓能較小,不足以使電纜地層測試器獲得精確的測量數據。
膨脹工具替代方案
采用配有壓力表的裸眼膨脹封隔器,已成為電纜地層測試工具的一個成熟替代方案。使用膨脹裸眼封隔器可以不受液壓能限制進行測試。雖然這種作業成本更高且風險更大,但這需要將其與應力預測不確定性帶來的成本進行權衡。
作業公司已成功利用裸眼膨脹封隔器來測量原始應力。經驗表明,當辦公室人員和井隊人員制定了詳細的作業計劃后,實際作業往往能夠取得成功。在最近的兩個案例中,作業公司在海上采用了裸眼膨脹封隔器來隔離和測量原始應力。
在一個案例中,使用了兩個封隔器的跨式配置,完成了應力的測量。這種配置相比僅采用一個封隔器而言,可以使工程師能夠更精確地確定測量的位置。測試的目的是測量原始應力,以便在井的整個生命周期內管理注入壓力。采用膨脹封隔器測量原始應力的基本操作是通過向地產注入流體,加壓并初步形成裂縫,同時保持恒定的注入速率。然后獲取裂縫傳播壓力和閉合壓力以確定應力數據。對于每個坐封深度,測試通常重復3次。
單封隔器案例研究
使用單封隔器配置,也可以實現同樣的裂縫傳播過程,然后測量關閉壓力。然而,使用單個封隔器,無法確定在封隔器下方裂縫開始形成的具體深度。對于一些作業人員來說,相比隔離不同井段獲得的更高精度,他們更看重采用單個封隔器,而不是兩個封隔器的低風險。該作業公司在一次深水作業中使用單個封隔器方法成功測量了原始應力,獲得了足夠的可用數據,以準確預測下一開套管鞋深度。與之前采用應力預估相比,通過避免下入額外的鉆井尾管,單封隔器應力測量作業節省了大量成本。
高膨脹元件
深水封井和棄置(P&A)作業時,通常在預棄井程序前,需要使用連續油管來完成所需的各種服務。很多時候,用于連續油管設備的BOP內徑比管柱的內徑小。在這種情況下,就需要使用高膨脹率的膨脹元件。通常來說,預棄井作業是指在動員鉆機進行完整的P&A作業前,進行產層隔離。使用連續油管裝置進行預棄井工作成本較合理且安全性高。采用連續油管完成初期作業可以確保井控安全。
案例分析
在一個多分支井項目中,需要在篩管上坐封橋塞,然后打水泥灰。坐封橋塞的套管為6-5/8in,其上為5-1/2in油管,如圖6。根據5-1/2in油管的最小內徑選擇了4-3/4in的膨脹工具。封隔器下到位后,打壓膨脹并坐封橋塞,如圖7。采用液壓丟手工具使送入工具與橋塞斷開,之后在橋塞頂打水泥灰。
水泥固化后,進行了壓力測試來評估水泥塞的壓力完整性,通常需要在地面打壓來完成此項工作。然而,在某些井,水泥橋塞之上壓力并不完整。在這種情況下,采用一個2.90-in外徑的多次坐封封隔器,坐封在橋塞之上進行壓力測試。

圖6.一個大規模P&A項目中的典型井的示意圖

圖7.封隔器位置圖和井內工具詳細圖
作業結果
總共成功完成了16口井的預棄井作業,使用連續油管下入膨脹橋塞。此項目的成功很大程度上得益于作業前詳盡的設計規劃。雖然工程師有意愿,但許多情況下,并非所有的相關人員都參與了設計過程。參與人員最好包括平臺工作人員、連續油管操作人員和負責下入膨脹工具的服務人員。他們的參與利于明確工作的重點環節并識別出關鍵的意外風險。在這種多分支井項目中,“做好充分的準備,再付諸行動”是明智之舉。
結論
在過去20年,膨脹工具的設計有了明顯的提高,技術的不斷研發使其應用范圍不斷擴大。在無法采用傳統的方法時,這些新的膨脹工具為作業公司提供了一種經濟有效的替代方案。選擇膨脹工具的首要原因是其可以克服使用標準工具的井眼限制;其他原因包括保護措施較弱,或者套管腐蝕,使用標準方法可能損壞套管。膨脹工具還具備在受限條件下的回收能力,而且對于大尺寸套管,在常規工具供應不足或者根本就沒有相應常規工具的情況下,膨脹工具可以有效解決問題。
您也有讓人撓頭的難題需要解決,或是優質技術想要找應用市場嗎?如果有的話,歡迎聯系小編微信或郵箱,也許能找到一劑良藥。
二丫:131-3255-0596;zhanglingyu@fonchan.com
大安:131-3203-1392;lishian@fonchan.com
For English, Please click here (展開/收縮)
MEASURING IN-SITU OPEN-HOLE STRESS
Knowing the in-situ stress of an open-hole section is desirable for several reasons. Firstly, stress values are crucial to managing an injection well to ensure that the injection zone maintains integrity with respect to cap rock strength and that no fractures are created that would allow injection fluids to go out-of-zone. In-situ stress measurements also help engineers select optimal casing shoe depths. Drilling teams are typically conservative when planning casing shoe depths when there is limited information or predictive modeling is used. However, setting casing early may drive-up well cost, or conversely, estimations may be aggressive which could lead to well control issues and implementing costly contingency plans.
The typical method used to measure in-situ stress is a wireline deployed formation testing tool. However, in wells with angles of more than 30° challenges arise due to the small volume of available hydraulic energy, which may not be sufficient for a wireline formation tester to gain accurate measurements.
Inflatable alternative. The use of an open-hole inflatable packer, equipped with pressure gauges, is a proven alternative to wireline formation testing tools. Using an inflatable open-hole packer allows access to unlimited hydraulic energy to perform the test since fluid is being pumped from surface. While this operation has a higher cost and poses greater risk, these must be weighed against the cost of the uncertainty in estimating stress.
Operators have successfully used open-hole inflatable packers to measure in-situ stress. Experience has shown that when office and rig personnel conduct detailed job planning, execution of the operation is successful. In two recent cases, companies working in an offshore environment used open-hole inflatable packers to isolate and measure in-situ stress.
Measurements were made in one case with a straddle configuration using two packers. This type of set-up enables engineers to determine exactly where the measurement was taken as opposed to when only one packer is deployed. The purpose of the test was to measure the in-situ stress to manage the injection pressure through the life of the well. The basic operation in measuring in-situ stress with an inflatable packer is to pressure up and initiate a fracture by injecting fluid into the formation while maintaining a constant injection rate. The fracture propagation pressure and closure pressure thus obtained are then used to determine the stress measurement. This test is typically repeated three times for each setting depth.
Single packer case history. The same process of propagating a fracture and then measuring the closure pressure was performed using a single packer configuration. However, with a single packer there is no way to determine at what depth below the packer the fracture was initiated. For some operators, the reduced risk of running one packer, rather than two, is more advantageous than the greater accuracy that comes from isolating an interval. This operator used a single packer approach in a deepwater application to successfully measure in-situ stress, deriving enough usable data to accurately predict the next casing point. The simplified operation generated substantial cost savings by eliminating an additional drilling liner compared to stress estimations used on previous wells.
HIGH EXPANSION ELEMENT
Deepwater plugging and abandonment (P&A) operations commonly use coiled tubing to deploy various services required in pre-abandonment procedures. In some instances, the BOP riser package for coiled tubing units can have an ID smaller than the ID of the pipe where an operation is to be performed. This restriction typically requires the use of a high expansion inflation element. Pre-abandonment work is often done to isolate production zones prior to moving in a rig to perform the full P&A procedure. Doing pre-abandonment work with a coiled tubing unit is cost effective and operationally safe. Doing the initial work on coiled tubing further allows complete well control to be maintained since the work is conducted through the existing wellhead.
Case study. A multi-well campaign was planned and required a bridge-plug be set above screens and cement dumped on top. The casing to set the bridge-plug in was 6 5/8-in. with 5?-in. tubing above. A 3?-in. inflatable element was selected based on the minimum restriction in the 5?-in. tubing. The packer was deployed to depth, and pressure was applied to inflate and set the plug. A hydraulic disconnect was used to release the tool from the plug, after which cement was spotted on top of the plug.
Once the cement had set, a pressure test was performed to assess the integrity of the plug. This typically was done by applying pressure at the surface. However, in some wells pressure integrity was lacking above the cemented bridge plug. In these cases, a multi-set packer with a 2.90-in. OD was run in the well to set just above the bridge-plug, to perform a pressure test.
Results
In all, 16 wells were successfully pre-abandoned, using inflatable plugs run on coiled tubing. Much of the success of this project was due to the detailed pre-job planning. While engineers have good intentions, in many cases not all stakeholders are included in the planning process. It is important to include platform workers, coiled tubing operators, and the actual service personnel responsible for running inflatable tools. Their input can highlight important details and identify critical contingencies. It is wise to “measure twice and cut once,” in this type of multi-well campaign.
CONCLUSION
Inflatable tool design has improved significantly over the past 20 years, and research and development is ongoing to extend the limits of the technology. These new inflatable tools provide operators with a cost-effective alternative method when a conventional approach is not possible. The primary reason for selecting an inflatable tool is to circumvent a wellbore restriction that prevents the use of a standard oilfield tool. Other reasons are to safeguard weak and/or corroded casing that might be damaged using standard methods. Inflatables also have the capability to retrieve a tool through a restriction, and efficiently handle large casing sizes where conventional tools may be in low supply or non-existent.
未經允許,不得轉載本站任何文章: