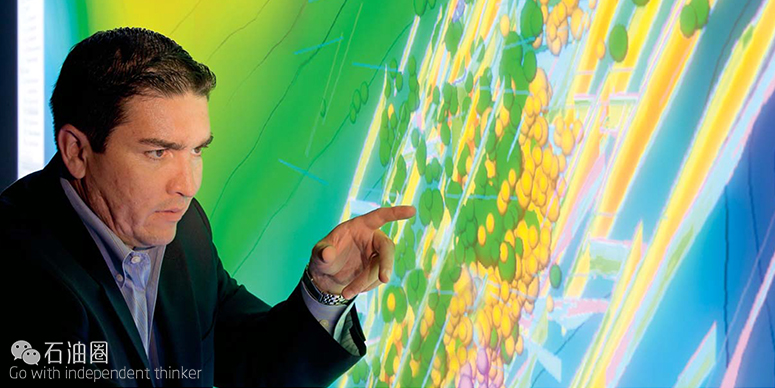
2015年三月,一種由Ziebel公司生產的重力式碳化復合電纜 — Z-Line在油氣行業中首次被用來獲取有價值的溫度分布數據和聲波光纖分布數據。Ziebel一次性安裝在井中可實現長期的井下數據監測,為油田生產提供全周期的保護。
Z-Line在挪威的海上油田得到了首次應用。整套系統配合標準的重力式電纜和干式封隔壓力控制設備(無油脂注入)被下入到一口平臺井的9684 ft(2952m)處。作業過程中系統各項機械指標正常,作業者獲得了質量極高的分布式光纖數據(DFO),這些數據對后續工作具有非常高的價值。
“我們非常高興地看到Z-Line在其第一口商業修井作業中的成功表現?!盳iebel的CEO Stig Hognestad說,“這標志著Ziebel團隊完整的開發過程和嚴格的測試取得了成功。除此之外,該技術的成功對我們以及整個行業的真正意義在于,它證明了Z-line系統的功能在實際的井眼壓力環境下獲得了預期效果。此次應用的成功,表明這項服務已可以為其他作業者服務?!?/span>
Z-Line是基于Z-System碳復合材料技術發展起來的,這項技術能夠幫油田公司獲取至關重要的井況信息。這兩者(Z-Line和Z-System)之間最主要的區別是Z-Line完成這些工作僅需更細的電纜,且是重力式的,通常單井修井作業時間更短。
Z-Line的直徑為3/16 in(4.8mm),光纖由碳復合材料所包裹。這種設計讓整條線纜上都可以進行分布溫度感應(DTS)和分布聲波感應(DAS)。另外,Ziebel的光點壓力和溫度傳感器包含在底部鉆具組合(BHA)中,裝置本身帶有一個連接扣,允許標準的存儲式測井工具接在BHA以下。Z-Line的安裝和配置與標準的套管井電纜測井配置一致,盡管分布式測量采集方法不同,其在井下工作時線纜處于靜止狀態。
應用與優勢
碳化復合材料使得線纜有著極高的強度重量比,與直徑接近的鋼纜或者繩纜相比,其抗斷強度(6,600lbs/3,000kg)要大很多。光滑的外表面加工使其能夠有效密封,對金屬的低摩擦系數以及線纜的相對剛度增加其下至斜井段的能力。另外,較小的摩擦力減小了磨蝕以及標準電纜和鋼絲作業引起的油管磨損。
Z-Line的應用
- 井筒完整性,生產井:環空滲漏檢測來源以及進行套管檢測后的流體運移;
- 井筒完整性,注入井:確保在過壓實區域沒有不必要的注入。決定需要進行修井作業還是繼續注入作業;
- 永久棄井:提供信息優化橋塞的個數,決定下入深度,確定套管切割位置,驗證井筒完整性;
- 生產優化:確定穩定生產井所需的氣舉參數以及最優的氣體注入體積/生產比率。驗證GLVs(氣舉閥)按正確的步驟操作且偏心堵塞器沒有泄露,優化的氣舉系統可以增加最多15%的產量,節約注氣成本。
技術優勢
- 低密度,高強度
- 井筒磨損低
- 應用范圍更廣
- 不影響井筒液體流動,提供的數據更真實
- 不需要注入控壓油脂
- 一次安裝,永久使用,提供長時間的數據保證
- 更好的聲學耦合效果
如需獲取關于該技術的更多資料,請聯系石油圈技術運營 Demons,QQ:2582825239。
作者/OE Staff ? ?譯者/白小明 ? ?編輯/Lemon
Stavanger-based Ziebel announced that for the first time in oil and gas history, the Z-Line, a gravity-deployed slim carbon composite cable, was used to acquire meaningful distributed temperature and distributed acoustic fiber optic data during a commercial well intervention.
The Z-Line made its inaugural run for a major operator offshore Norway.? The system accessed a platform well to a depth of 9684ft with standard wireline-type gravity deployment and dry sealing pressure control equipment (no grease injection).? All mechanical requirements of the line functioned successfully, and high quality distributed fiber optic (DFO) data was acquired for the operator.
“We are very pleased with the Z-Line’s successful performance during its first commercial well intervention,” says Stig Hognestad, Ziebel CEO. “It marks the culmination of a thorough process of development and rigorous testing by the Ziebel team.? The real significance for us – and the industry – is that it proves that the system functions as intended in an actual live pressured well environment.? With the success of this launch, the service is now available to all operators.”
Z-Line builds upon the proven Z-System carbon composite technology, which delivers critical decision-making well information to oil companies.? The key difference between the two is that the Z-Line does so from a smaller wireline footprint, and, being gravity deployed, with a typically shorter intervention time per well.
The Z-Line is a 3/16 in. (4.8mm) diameter carbon composite line with embedded optical fibers at its core.? This enables distributed temperature sensing (DTS) and distributed acoustic sensing (DAS) to be performed along the full length of the line.? In addition, Ziebel’s optical point pressure and temperature sensors are contained within the bottom hole assembly (BHA), along with a connection to enable standard memory logging tools to be run below the BHA.? The rig-up and footprint are similar to that of a standard wireline cased-hole setup, although the distributed measurement acquisition method does differ in that it is carried out with the line parked stationary in the well.
The carbon composite material enables the line to have an extremely high strength-to-weight ratio, with a breaking strength (6,600lbs/3,000kg) well in excess of what can be achieved with a similar diameter of steel wire or braided line.? The smooth outer finish makes for effective sealing, and the low friction coefficient to steel plus the relative stiffness of the line gives it increased ability to reach into deviated wells.? In addition, the low friction reduces the abrasion and tubing wear associated with standard wireline or slickline runs.
Z-Line applications
Applications that can be addressed with the service include:
- Well Integrity, producers: annular leak detection source and fluid migration behind casing detection.
- Well Integrity, injectors: verify that no unwanted injection occurs into the overburden.? Decide, with confidence, whether remedial work is required or to resume injection.
- P&A: provide information to help optimize the number of plugs and to decide where they should be set, to determine where to safely cut casing strings, and to verify wellbore integrity.
- Production optimization: determine gas lift settings required for a stable flow regime and the optimal gas injection volume/production ratio.? Verify that GLVs operate in the right sequence and that dummy valves are not leaking.? An optimized gas lift system can increase production by up to 15% and save gas injection costs.
未經允許,不得轉載本站任何文章: