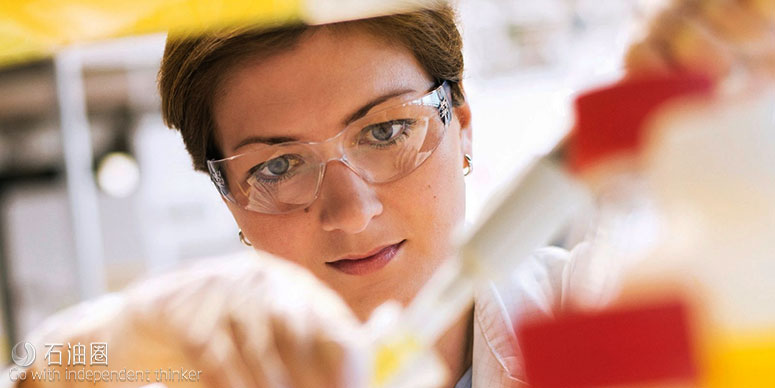
本文將討論新型耐鹽減阻劑體系在Marcellus頁巖的現場試驗。
來自 | JPT
編譯 | 白小明 影子
無論是用于滑溜水壓裂還是連續油管增產,減阻劑都可提高泵送水排量,同時維持較低的處理壓力。通常而言,常規丙烯酰胺/丙烯酸共聚物或部分水解的聚丙烯酰胺基FR的性能隨著源水的溶解離子含量增加而減小,并且還取決于源水中的離子類型和濃度?;诖讼拗?,用于滑溜水壓裂作業的返排水和產出水通常需要用淡水來稀釋以保持足夠的減阻性能。為了100%利用產出水,已開發的新型減阻劑可讓總溶解固體含量(TDS)超過300,000ppm的返排水和產出水得到近乎淡水的性能。
新型耐鹽減阻劑(FR)體系設計用于特定的高鹽度范圍,可在滑溜水水力壓裂應用中100%利用返排水和產出水,無需用淡水進行稀釋。耐鹽FR服務可用于TDS大于300,000ppm的情形;其在不同溶解鹽離子的水中有效,這些離子包括氯化物、硫酸鹽、鈉、鈣和鎂;它還能適用于各種未知的、可能會使傳統的FR失效的污染物。低濃度(0.25~1加侖/1,000加侖)的新型FR體系在粘土控制鹽水、返排水和產出水中仍可起作用。
這種新型耐鹽減阻劑體系包含一種油包水陽離子聚合物和反相劑。與其他FR不同,新型減阻劑的獨特優勢在于,聚合物與反相劑的比例可以隨時進行調整,以最大程度減小摩阻。在泵送作業期間,反相劑被證實能夠迅速將聚合物從油中釋放到水中實現相反轉,并且陽離子聚合物即使在污染嚴重的水中,也能非常有效地減少多余的套管摩阻。此外,使用單一的FR可減少產品庫存,簡化現場材料使用的質量控制。
流動回路測試
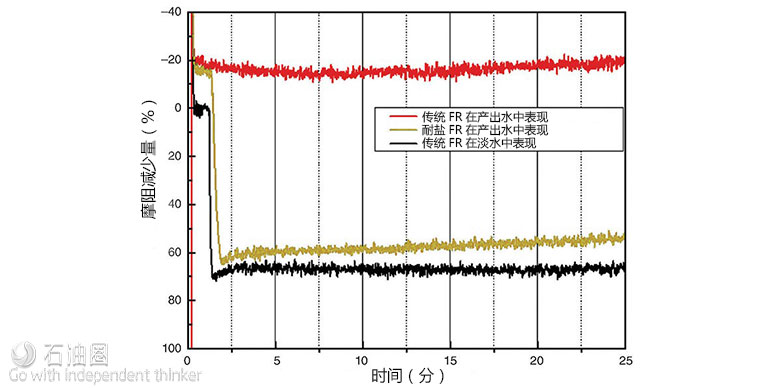
圖1.新型FR在總溶解固體含量為200,000ppm的水中表現優于傳統的FR。
通常,在實驗室進行摩阻回路測試來確定各種FR的性能。該測試能夠顯示FR在處理或源水中的減阻情況,這將最終影響處理壓力和增產處理期間對液壓水馬力的要求。然后將這些數據與傳統FR在淡水中的數據進行比較,得出結論。圖1顯示了新型耐鹽FR的性能。與傳統的FR相比,對現場供水水源,新型耐鹽FR表現出更優越的性能。這些結果表明,耐鹽減阻劑能夠在壓裂作業中使用無需稀釋的返排液和產出水,從而減少了(用于稀釋的)水的額外開支和物流成本,這些水最終將被視為廢棄物而進行處理。此外,使用這種化學液體能夠重復使用返排液和產出水,這將是經濟、環境可持續的解決方案。
在現場實際泵送過程中,管道的減阻效果受FR載荷、FR有效性,以及FR在壓裂液中的分散性等多個參數影響。特別是FR的化學性質非常重要。最常用的陰離子FR,如部分水解的聚丙烯酰胺,傾向于在高含TDS的水(如TDS大于60,000ppm的水)中聚集結塊、無法完全伸展,這將使減阻效果變差。然而,陽離子減阻劑可以克服這一難題,因為它們受陽離子(與壓裂液中的TDS含量直接相關)的影響較小。換句話說,它們仍然可以在一定程度上伸展和延伸。
現場試驗
通常,作業人員會以較高的排量泵送滑溜水體系以覆蓋壓裂設計指定的巖石范圍。當FR在平均處理排量(ATR)、平均處理壓力(ATP)下不能充分減阻時,通常會提高FR濃度。與常規FR相比,這種耐鹽陽離子減阻體系無需提高濃度,可采用較低的處理壓力和泵送排量。作業人員在Marcellus頁巖進行了三口井的現場試驗。
1號井,壓裂前10段采用傳統的FR,之后采用耐鹽FR。ATP和ATR立即作出響應,ATR基本維持在大于90桶/分鐘的水平。在第20段作業期間,ATR下降到90bbl / min以下,這是由于操作人員在作業中調整了耐鹽FR和反相劑的比例。
2號井,前14段泵入現場標準的陰離子減阻劑。ATP維持較高水平,并在8,700和9,100 psi之間波動。當從第15段壓裂開始,切換為耐鹽FR后,ATP立即下降到8,100psi,并保持在8,000~8,700psi之間,波動主要是由于在作業中調整FR和反相劑比例造成的。另外,ATR在轉換成耐鹽FR后即刻增至100桶/分鐘,并在其余各段保持了這一排量。
如果把常規減阻劑和耐鹽減阻劑體系的ATP看作是受污染水重量百分比的函數,那么數據表明耐鹽減阻劑即使在水100%受污染的情況下,仍能保持相對較低的處理壓力(小于9,000psi)。對ATR而言,數據充分表明,即時針對100%的受污染水,與現場標準FR相比,耐鹽FR體系也能夠將處理排量提高至100桶/分鐘。
通過對比各段常規FR和耐鹽FR體系的濃度,結果表明耐鹽FR即使濃度低于1加侖/ 1,000加侖,仍能能保持較高的泵送排量。
結論
在滑溜水壓裂作業中,作業人員配制并泵送了一種耐鹽減阻劑,100%利用了產出水。與常規FR相比,ATP維持在較低水平,ATR維持在較高水平。此外,在大多數泵送階段,耐鹽FR濃度保持在1加侖/ 1000加侖以下。通過調整反相劑的用量,耐鹽減阻劑體系可根據需求進行定制,這提高了100%使用產出水應用環境下的減阻效果。
您也有讓人撓頭的難題需要解決,或是優質技術想要找應用市場嗎?如果有的話,歡迎聯系小編微信或郵箱,也許能找到一劑良藥。
二丫:131-3255-0596;zhanglingyu@raiborn.com
大安:131-3203-1392;lishian@raiborn.com
For English, Please click here (展開/收縮)
To continue to treat multiple clusters in longer laterals effectively, even for stages near the toe, a robust friction-reducer (FR) system typically is required to overcome pipe friction. Additionally, using a single FR system throughout the entire treatment that can tolerate various water sources of varying salinity up to 300,000 ppm is imperative. This paper discusses the field trials of a new salt-tolerant FR system in the Marcellus Shale.
Introduction
FRs are used to enable high-rate pumping of water while maintaining lower treating pressures in both slickwater fracturing and coiled-tubing stimulation applications. Typically, the performance of conventional acrylamide/acrylic acid copolymer or partially hydrolyzed polyacrylamide-based FRs diminishes as the dissolved-ion content of the source water increases and can be dependent on both the type and the concentration of ions present in the source water. Because of this limitation, flowback and produced water used for slickwater applications are often diluted with a freshwater source to maintain adequate friction-reducing performance. To enable the use of 100% produced water, new friction reducers have been developed that are capable of providing near-freshwater performance in flowback and produced water exceeding 300,000 ppm total dissolved solids (TDS).
The new salt-tolerant FR consists of FR systems that are designed to work in a specific range of high salinity to enable the use of 100% flowback and produced water in slickwater hydraulic-fracturing applications without requiring dilution with fresh water. The salt-tolerant FR service can handle TDS levels greater than 300,000 ppm; is effective in water containing a variety of dissolved salt ions, including chlorides, sulfates, sodium, calcium, and magnesium; and can tolerate a variety of unknown contaminants that might render conventional FRs ineffective. The new FR system is effective at low concentrations (0.25 to 1 gal/1,000 gal) in clay-control brines and flowback and produced-water sources.
This new salt-tolerant FR system consists of a water-in-oil cationic polymer and an inverter. Unlike other FRs, the distinctive advantage of the new FR is that the ratio of polymer to inverter can be readily adjusted on the fly to achieve maximum friction reduction. During the pumping operations, it was demonstrated that the inverter was sufficiently quick to invert and release the polymer from oil to water and the cationic polymer was extremely efficient at reducing additional pipe friction, even with severely impaired water. Additionally, the use of a single FR reduces inventory stock and simplifies on-location quality assurance of material usage.
Flow-Loop Tests
Laboratory friction loop testing is typically conducted to determine the performance of various FRs. This testing provides an indication of the friction reduction of the FR in the treatment or source water, which ultimately will affect treating pressures and the hydraulic-horsepower requirements during a stimulation treatment. These data can then be compared with those from conventional FRs in fresh water, and a conclusion can be drawn. Fig. 1 above displays the performance of the new salt-tolerant FR. The new salt-tolerant FR displayed superior performance in field-supplied water sources compared with the conventional FR. These results show that salt-tolerant FRs enable the use of undiluted flowback and produced water in fracturing operations, consequently reducing the need for excess expenses and logistics for water that otherwise would be considered waste stream for disposal. In addition, the use of this fluid chemistry enables recycling of flowback and produced water, which can be economically and environmentally sustainable solutions.
During actual pumping on location, the pipe friction reduction is affected by several parameters, such as FR loading, FR effectiveness, and how well the FR is dispersed in the fracturing fluid. In particular, the chemistry of the FR is crucial. Most commonly used anionic FRs, such as partially hydrolyzed polyacrylamides, tend to agglomerate and do not stretch fully in high-TDS water (e.g., water with greater than 60,000 ppm TDS), which results in poor friction reduction. Cationic FRs, however, can overcome this challenge because they are less affected by the presence of cations, which directly correlates to the TDS level in the fracturing fluids. In other words, they can still stretch and extend to some extent.
Field Trials
A slickwater system is typically pumped at higher rates to cover the rock volume as specified in the fracture design. When the FR does not provide sufficient reduction in the average treating pressure (ATP) at the average treating rate (ATR), the FR concentration is usually increased. This salt-tolerant cationic FR system does not require increasing the concentration yet allows lower treating pressures and pumping rates compared with conventional FRs. A three-well trial was executed in the Marcellus Shale.
For Well 1, the conventional FR was pumped for the first 10 stages, after which the FR was switched to the salt–tolerant FR. Both the ATP and the ATR immediately responded, and an ATR greater than 90 bbl/min was largely maintained. During the 20th stage, the ATR dipped below 90 bbl/min, which is attributed to the operator adjusting the ratios between the salt-tolerant FR and the inverter on the fly.
For Well 2, the field-standard anionic FR was pumped for the first 14 stages. The ATP remained high and fluctuated between 8,700 and 9,100 psi. As soon as the conventional FR was switched to the salt-tolerant FR at the 15th stage, the ATP immediately dropped to 8,100 psi and remained between 8,000 and 8,700 psi, with the fluctuations resulting from the ratios between the FR and the inverter being adjusted on the fly. In addition, the ATR increased to 100 bbl/min -immediately after the switch and was maintained at that rate for the remaining stages.
When looking at the ATP for both the conventional FR and the salt-tolerant FR system as a function of the weight percentage of impaired water, the data illustrate that the salt-tolerant FR was able to maintain relatively low treating pressure (less than 9,000 psi) at 100% impaired water. In terms of the ATR, the data strongly suggest that the salt-tolerant FR system was able to raise the treating rate to 100 bbl/min compared with the field-standard FR, despite the use of 100% impaired water.
Comparing the FR concentrations at each stage for the conventional and salt-tolerant FR systems, the salt-tolerant FR generally maintained a higher pumping rate, even at a concentration lower than 1 gal/1,000 gal.
Conclusions
A salt-tolerant FR system was formulated and pumped in slickwater fracturing treatments with up to 100% produced water. The ATP was maintained lower and the ATR was maintained higher compared with those observed with the conventional FR. Furthermore, the salt-tolerant-FR concentrations, for most of the pumped stages, were maintained below 1 gal/1,000 gal. The salt-tolerant FR system is customizable through independent inverter dosage, which results in improved friction-reduction performance for use in 100%-produced-water conditions.
未經允許,不得轉載本站任何文章: