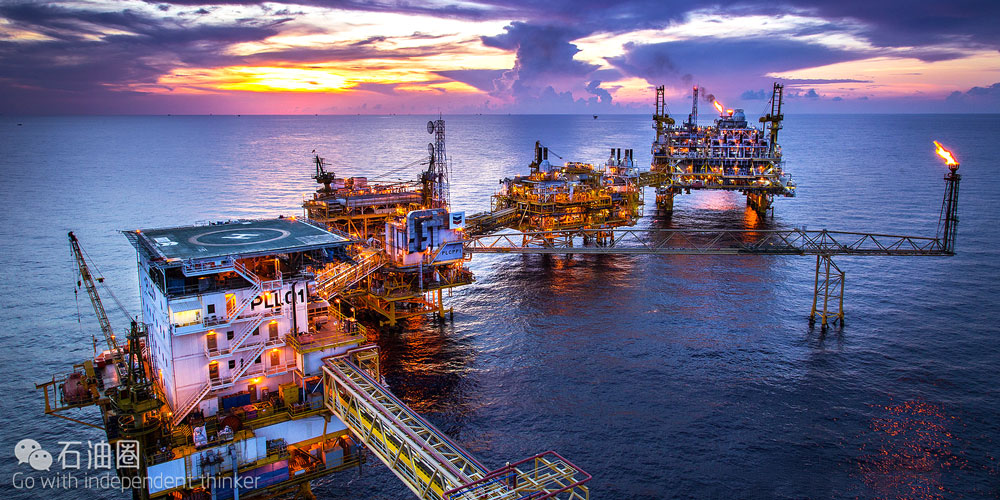
日前,高溫高壓井數逐漸增加,對完井工藝也提出了更高的要求,本文主要指出了高溫高壓完井修井工具的發展狀況,并討論了井身設計以及產品開發所面臨的挑戰。
高溫高壓工具的應用方式正在不斷的發展變化,研發周期正在延長,特別是針對超高溫高壓(超過壓力15,000psi或者溫度超過350°F)情況下的高溫高壓工具,研發周期更久,這些適用于超高溫高壓的工具,需要篩選制作材料并進行穩定性評估。
高溫高壓下完井技術的特殊挑戰
高溫高壓環境下的完井技術面臨著多種多樣的挑戰,并且挑戰還在持續增加。此前對高溫高壓項目的調查顯示在封隔器、橋塞、尾管掛、井下安全閥、油管-封隔器密封和其他相關產品方面存在著技術空缺。
除了材料設計和高溫高壓環境測試方面,在其他專門基礎元件方面也面臨很大的挑戰。
封隔器:封隔器和橋塞已發展到能夠用于500°F和25,000psi的井下條件,但在目前發展過程中的主要困難在于金屬和非金屬材料的可用性,這些材料需要適用于非常高的應力和應變條件,并且這些材料需要有較好的抗腐蝕性,以保證長期有效。石油圈原創www.h29736.cn
井下安全閥:井下安全閥包含了許多動態密封裝置,在整個完井周期中這些密封裝置都必須保持完整性和操作性能穩定。并且作業者可通過使用內插閥來延長有故障的安全閥的使用周期。內插閥是通過鋼絲作業下入的更小內徑的閥,能夠插入到油管連接的安全閥內部密封桶內,以此能夠在安全閥失效的情況下保持生產。
尾管懸掛器:帶有完整密封性的尾管懸掛器已經成功開發并應用于高溫高壓環境。一般來說,這些工具需要起到密封作用才能達到氣密性的要求,但是針對尾管懸掛器的行業標準尚未制定出來。
電子元件:常規工業用和軍用電子元件的耐溫能夠達到125℃,這遠低于高溫井下電子元件使用的耐溫要求,比如MDW和旋轉導向系統中使用的電子元件。盡管這樣,在高溫應用方面,石油天然氣行業井下工具仍然是時間最久和規模最大的電子元件用戶。石油圈原創www.h29736.cn
智能監控和生產系統:電子系統和光纖系統在井下監控方面已經得到了應用。市面上的電子監控系統已經可以應用到150°C和30,000 psi的環境下,并且平均使用壽命能夠達到10年?,F在能夠適應更高溫度下的版本在175°C和30000psi環境中,平均使用壽命為5年?,F在市面上的光纖系統能夠達到耐溫536°F以及耐溫20, 000psi。光纖系統一個非常重要的特點是它不含電子元件,因此與電子元件相比,光纖系統在更高的溫度下更可靠并且使用壽命更長。
智能生產系統指智能井系統,包括流動控制閥、儀表、化學藥劑注入閥和其他工具。這些工具用來控制儲層生產并且作為監控系統的平臺??傮w來說,這些系統已經升級到“近高溫高壓”狀態。市面上銷售的電子系統能夠耐壓高達15,000psi,平均使用壽命高達20年,但是只適用于次級高溫高壓條件。
高溫高壓下修井技術的特殊挑戰
一直以來,有關技術缺口和挑戰方面的討論都是圍繞著完井工具和系統。但是,在井筒干預方面也存在著巨大的挑戰。石油圈原創www.h29736.cn
一些墨西哥灣的作業者已經開始在超高溫高壓環境下使用先進的永久式橋塞作為獨立密封工具。這些先進的永久式橋塞(有時指隔離橋塞)集成了橋塞和生產封隔器的技術,以滿足超高溫高壓條件下對井下隔離和井使用壽命的要求。
油管切割器:現在業內有許多種類的油管切割器。它們其中的一些可以有效應用在超高溫高壓環境中,但是很少能夠保持持續的有效性。噴射式切割器用聚能射孔彈進行切割??梢允褂迷S多種類的射孔彈,并且這些射孔彈的耐溫級別與射孔槍基本一致。
化學切割是通過工具本體上的小孔噴射化學藥劑。在高壓環境下,化學切割的有效性因回壓對化學切割液的影響而降低。在高溫高壓環境下,化學切割的效率低于50%。
等離子切割器使用帶電等離子體進行切割,目前的耐溫耐壓級別分別是500°F 和 20,000 psi。
機械切割器由于受電子元件和裝有電子元件的襯套的影響,其耐溫耐壓性能有限。目前的技術條件下,機械切割器能夠用于392°F 和 20,000 psi的環境條件。機械切割器能夠實現可控切割并且產生較細的碎屑,并且從地面進行控制,能夠實現實時調整。
測井儀器和電子元件:在高溫高壓環境下,PCB (printer-circuit-board)的使用壽命是非常有限的。在超過150°C的環境下,PCB的壽命是以小時計的。一些新型的測井工具使用混合或者多芯片模塊,能夠耐溫175°C,使用壽命也只能夠以天計。當溫度超過175°C時,電子元件的使用受限于一些無源測井工具,使用壽命以小時計。這些工具可以進行降溫,以延長其使用壽命。
其他挑戰:在井筒干預方面,高溫高壓環境下的數據傳輸和工具打撈方面還存在更多的挑戰,包括作業管柱的限制、封隔器的回收、正向頂替馬達的溫度限制和投球坐封工具的溫度壓力限制。
井身設計石油圈原創www.h29736.cn
系統綜合測試:對許多應用來說,綜合測試是非常具有挑戰性的,但也是對完井或者修井作業至關重要的。例如,對于一個高溫高壓橋塞、高溫高壓水力坐封工具和一個高溫高壓套管接箍定位器來說,他們都能夠進行單獨測試,但是把他們集成起來作為一個系統在井下環境中進行測試可能就會變成一個嚴峻的考驗。
傳輸方法:可以采取多種不同的方法把工具下入井中,包括油管、連續油管和電纜(鋼絲作業和電纜)。選取的傳輸方式取決于許多因素,也決定了地面設備如何配置。對于較深的井,一般首選電纜,因為這種方式能夠極大的縮短作業時間。石油圈原創www.h29736.cn
風險和可操作性分析:風險和可操作性分析用于在作業中識別風險和作業問題。正確的識別潛在風險和作業問題、制定方案和分析不同方案優缺點能夠有效的防止井控失效和保證人身安全。在高溫高壓環境下,風險和可操作性分析會有助于識別出那些在作業之前需要改進或者測試的工具。
監管條例總覽
全球各地監管條例各不相同,以下將講述一些安全和環境執法局對美國墨西哥灣水域的要求。
深水作業計劃:無論水深多少,所有的高溫高壓完井都需要進行深水作業計劃。安全和環境執法局要求任何復雜的、需要高級別專業知識的新技術都要經過第三方的審核。如果新技術超過了現有標準的限制,行業專家與安全和環境執法局必須經過討論、達成一致。如果新技術與現有的工程標準沖突,那么執法局會拒絕使用新技術。
高溫高壓新技術深水作業計劃:執法局建議作業者就高溫高壓項目的問題盡早聯系執法局的技術評估部門來接受最新的指導。對于任何新技術,理論作業計劃中都必須包含用于高溫高壓環境下的完整工具和材料清單資料,以及用于評估材料選擇、設計驗證分析和執行驗證測試的工程標準。新技術發展完成之后,最終作業計劃必須包含理論作業計劃里涉及的所有的分析和測試報告。
設計驗證和分析: API PER 15K和API 17TR8為執法局承認的作為高溫高壓材料選擇、設計驗證分析和測試的指導標準。
來自/JPT ?譯者/王凱 ?編輯/王亞釩
The methods used for highpressure/high-temperature (HP/HT) tool development are evolving, and development cycles are lengthening, particularly for ultra-HP/HT applications (those involving pressures greater than 15,000 psi or temperatures greater than 350°F) in which materials screening and stability assessments are required. What can the industry anticipate for future HP/HT wells in terms of architecture, product development, and regulatory challenges? This paper identifies current development paradigms and discusses the future challenges in well planning, product development, and regulation.
The technological challenges associated with the completion of wells at and above HP/HT conditions are diverse and continue to increase. Previous investigations into HP/HT projects identified technology gaps related to packers, bridge plugs, liner hangers, subsurface safety valves (SSSVs), tubing-to-packer seals, and related products. (Please see the complete paper for a comprehensive list of challenges faced in HP/HT environments, as well as a discussion of the historical perspective in HP/HT well development.)
In addition to the general challenge of materials design and testing for HP/HT environments, several specific component-based challenges also exist.
Packers. Packers and bridge plugs have been developed for service conditions as challenging as 500°F and 25,000 psi, but the primary difficulty in the development process today is the availability of materials, both metallic and nonmetallic, which are suitable for very high levels of stress and strain and which possess the desired corrosion resistance to achieve longevity requirements.
SSSVs. SSSVs contain many dynamic seals which must maintain their integrity and operating characteristics over the life of the completion. Also, the operator must have the capability to extend the life of a malfunctioning safety valve through the use of “insert valves.” These are smaller-diameter wireline-conveyed valves that can be run and inserted into the bore of the tubing-mounted safety valve so that production can continue under fail-safe conditions.
Liner Hangers. Liner hangers with integral packoff capabilities (packer-type expandable seals) have been developed for HP/HT applications. Typically, these tools are required to perform their sealing role to a gas-tight requirement. However, an industry specification tailored for the operational role of liner hangers does not yet exist.
Electronics. Conventional industrial and military electronic components are typically rated only to 125°C, far below the rating required for HT downhole electronics applications such as measurement-while-drilling and rotary-steerable systems in which they are used. Despite this, the oldest and largest consumer of electronics for HT applications is the downhole oil and gas industry.
Intelligent Monitoring and Production Systems. For downhole monitoring, electronic systems and fiber-optic (FO) systems are available. Electronic monitoring systems are marketed for use at 150°C and 30,000 psi, at which life expectancy is 10 years. Higher- temperature versions are currently marketed for use at downhole conditions as high as 175°C and 30,000 psi. At these conditions, life expectancy is only 5 years. FO monitoring systems are currently marketed for temperatures as high as 536°F at 20,000 psi. An important feature of FO systems is that they contain no electronic components; hence, they can operate reliably at much higher temperatures than electronic systems, and for much longer periods of time.
Intelligent production systems, sometimes referred to as intelligent-well systems, consist of flow-control valves, gauges, chemical-injection valves, and other components, and are used to control zonal production and act as platforms for monitoring systems. In general, these systems have been upgraded to “near-HP/HT” status. Commercially available electric systems on the market are rated for pressures up to 15,000 psi, but for sub-HP/HT temperatures, with life expectancy as high as 20 years.
HP/HT Challenges Specific to Well Intervention
Historically, discussions regarding technology gaps and challenges tend to focus on completion tools and systems. However, there are also significant challenges in well intervention.
Redundancy in Shoe-Track Isolation. Several Gulf of Mexico (GOM) operators have recently used advanced permanent bridge plugs for standalone barrier applications in ultra-HP/HT conditions to achieve redundancy in shoe-track integrity. These advanced permanent bridge plugs (sometimes referred to as isolation plugs) combine bridge-plug and production-packer technology to satisfy the need for ultra-HP/HT shoe-track isolation and life-of-the-well longevity.
Tubing Cutters. A variety of tubing cutters are available commercially. Some are effective into the ultra-HP/HT region, but few are known to be consistently effective in these applications. Jet cutters use a shaped-charge explosive to make the cut. A variety of charges can be used, and these models will be subject to (approximately) the same temperature limitations as perforating guns.
Chemical cutters operate by spraying a chemical through small ports in a tool body. In HP environments, their effectiveness is reduced by the backpressure effect (high hydrostatic pressure) on the chemical cutting fluid. At HP/HT conditions, chemical-cutter efficiency is well below 50%.
Radial torch cutters use energized plasma to make a cut. They are currently rated up to 500°F and 20,000 psi.
Mechanical cutters are limited by temperature because of the electronics and pressure owing to the housings that carry the electronics. Current technology can operate at 392°F and 20,000 psi. Mechanical cutters provide a controlled cut and generate only fine debris. The cut is controlled at surface, with the ability to modify the cut in real time.
Logging Tools and Electronics. Service life for printer-circuit-board (PCB) -based electronics packages at HP/HT conditions is very limited; at temperatures greater than 150°C, PCB life is measured in hours. A few new logging tools use hybrid or multichip modules and are rated at 175°C; their longevity is measured in days. At temperatures greater than 175°C, electronics usage is currently limited to a few passive logging tools, and longevity is measured in hours. These tools are passively cooled, which explains their short life span.
Miscellaneous Challenges. Several further significant intervention challenges exist in conveyance and fishing in HP/HT conditions, including work-string limitations, packer removal, temperature limitations of positive-displacement motors, and pressure and temperature limitations of ballistic setting tools.
Well Planning
Systems-Integration Testing. Systems- integration testing for many applications can prove challenging, but is critical to the success of the completion or intervention. For example, an HP/HT bridge plug, HP/HT nonballistic hydrostatic setting tool, and an HP/HT casingcollar locator can each be validated separately, but integrating them and testing them as a system at downhole conditions is the so-called “acid test.”
Conveyance Methods. There are several methods to convey tools into a well. These methods include pipe, coiled tubing, and wireline (slickline and electric line). The decision to use one method over another will depend on many factors and will determine how the rig must be configured for the operation. At greater depths, it is preferred, when possible, to use wireline because this can reduce rig time significantly.
Hazard and Operability (HAZOP) Analysis. A HAZOP analysis is used to identify hazards and operational problems that may occur during well operations. Identifying potential hazards and operational problems correctly and having a plan in place and knowing the advantages and disadvantages of various options can ultimately help prevent loss of well control and can save lives. In an HP/HT application, a HAZOP analysis may prove useful in identifying contingency tools that need to be developed or tested before use in a well.
The Regulatory Landscape
Regulatory requirements vary globally and are beyond the scope of this paper. Instead, this section describes some of the Bureau of Safety and Environmental Enforcement (BSEE) requirements for US GOM waters.
Deepwater-Operations Plan (DWOP). All HP/HT completions require a new technology (NT) DWOP, regardless of water depth. BSEE regulators require that any NT that is technically complex, and that requires a high degree of specialized knowledge, be reviewed by an independent third party. If the NT exceeds the limit of existing standards, industry experts and the BSEE must discuss the matter and achieve a high degree of convergence. If the NT conflicts with existing engineering standards, the BSEE will not approve its use.
NTDWOP Process for HP/HT Applications. The BSEE recommends that the well operator contact the Technical Assessment Section of the BSEE as early as possible concerning an HP/HT project to receive up-to-date guidance. For any NT, an NT Conceptual DWOP must be submitted with a complete list of all equipment and materials that will be used in the HP/HT well along with the proposed engineering standards that will be used to evaluate materials selection and design-verification analysis, and perform validation testing. After the development of the NT is complete, the NT DWOP submittal must contain all the analysis and test reports proposed in the NT Conceptual DWOP (see the complete paper for a description of these elements).
Design Verification and Analysis. The BSEE currently defaults to API PER 15K and API 17 TR8for guidance on HP/HT material selection, design-verification analysis, and validation testing. However, the BSEE does not consider these documents to be all-inclusive or complete.
未經允許,不得轉載本站任何文章:
-
- 檸檬
-
石油圈認證作者
- 畢業于中國石油大學(華東),油氣井工程碩士,長期聚焦國內外石油行業前沿技術裝備信息,具有數十萬字技術文獻翻譯經驗。如需獲取更多技術資料,請聯系我們。