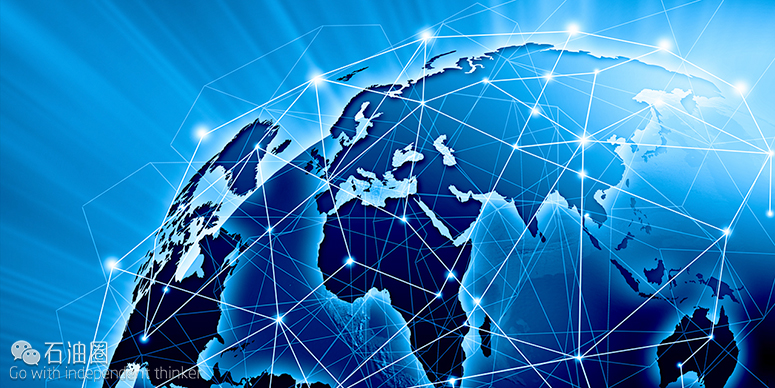
傳感器網絡綜合了傳感器技術、嵌入式計算術、計算機及無線通信技術、分布式信息處理技術,能夠通過各類集成化的微型傳感器以協作方式實時監測、感知和采集各種環境或監測對象的信息, 通過嵌入式系統對信息進行處理, 并通過自組織無線通信網絡將所感知的信息傳送到用戶終端。
無線傳感網絡可以定義為通過無線連接,利用安裝在各地的傳感器收集數據,并通過終端節點進行數據通信的網絡。根據通信架構的不同,數據可以直接發送至網關,或通過多個終端節點返回網關。之后,網關可以連接到其他設備或有線網和無線以太主干網,將傳感器信息傳遞到控制系統。
無分行業類別,這些網絡可以用于監測各類工況,幾乎覆蓋所有過程控制參數,包括但不僅限于壓力、流量、溫度和液面。
無線傳感網絡(WSNs)的出現,對那些想要獲得行業競爭優勢的油氣公司來說可謂是一項關鍵技術。WSNs出現以來,OleumTech等許多制造商對產品進行了改進,產品性能得到了大幅提升,可應用于惡劣環境。同時,針對該技術,OleumTech還改良了通信架構和安全體系,提高了設備可靠性,降低了電量消耗。
在整個油氣產業鏈(包括上、中、下游)以及電力、水/廢水處理以及制造業等領域的行業市場,無線傳感網絡正逐漸取代行業標準的電纜傳輸網絡,使用范圍越來越廣。
OleumTech公司OEM&戰略部副總裁Brent E. McAdams稱,“據統計,在多數行業應用中,無線設備的成本還不足有線設備的十分之一。而正是由于無線網絡在設計、施工、物流方面可以節約大量成本,同時借助于數據傳輸頻率和可靠性的提升,無線傳感網絡相關項目的啟動和盈利進度變得更快?!?/span>

油氣行業是使用無線傳感網絡最多的行業,通常部署在偏遠的地形條件惡劣的地區、海拔較高的地區、極端天氣地區。從油罐到壓縮機,從發電機到分離器和井口,無線傳感網絡可用于監測、管理和控制各種設備儀器。石油圈原創www.h29736.cn
隨著運營成本的不斷增加,同時油價已經跌至近8年的新低。在有線網絡費用太高或者不適用的地區,與傳統的有線網絡相比,無線傳感網絡無疑具有著無與倫比的優勢。
無線技術在應用上不斷取得進展,使企業得以告別有線網絡,進而部署費用更低的無線網絡。無線傳感網絡可以包含不同的傳感器,涵蓋大部分行業應用,如壓力、溫度、流量、液面高度或者只是簡單地通過離散發射器傳遞閉合信號。石油圈原創www.h29736.cn
無線傳感網絡主要應用于監測近實時過程控制數據、安全、監管和生產信息。
“由于替換電池不方便,如何進行‘能量采集’成為油田無線傳感網絡設計的關鍵因素;替換部署在偏遠地區的無線傳感器節點上的成千上萬塊電池,是一項成本昂貴令人頭疼的工程?!?/span>
無線傳感器終端節點可以使用多種能源形式,太陽能、機械能、熱能是主要的驅動能源。其中太陽能是使用最多、采集方式最復雜的能源。數據發送的頻率直接影響著能量的消耗。對于特定的監測應用,如監測油罐液面,延遲不是主要問題,而可靠性至關重要。石油圈原創www.h29736.cn
McAdams稱,“受各行業對先進技術方案強烈需求的驅動,為了提高生產率、效率和盈利性,眾多企業紛紛開始采用無線傳感網絡。正是數據技術對創新的驅動,才使作業者有能力提高對過程的控制,降低成本,提高效率,做出更好的決策,滿足運營商的特殊需求?!?/span>
小編手中還握有無線傳感網絡技術等其他產品的更多資料哦,想獲???很簡單:請將此文章分享至朋友圈,發送截圖和郵箱地址至石油圈微信后臺。小編會將資料打包奉上,發送至您的郵箱!還有機會與技術專家溝通交流哦~
來自/OleumTech ? 譯者/白小明 ? 編輯/Leia
Wireless Sensor Networks (WSNs) have emerged as a key technology for oil and gas exploration and production companies looking to gain a competitive advantage. Since initially introducing WSNs, manufacturers like OleumTech have enhanced product offerings to operate in the most inhospitable of environments while fortifying the technology with more robust communications architectures, hardening security, increasing reliability, and driving down power consumption. Through the entire oil and gas value chain (upstream, midstream, and downstream) as well as other industrial markets including electric power, water/wastewater, and manufacturing, wireless sensor networks are increasingly being deployed where hardwiring was the de facto standard.
“For many industrial applications, it has been well documented that wirelessly connected assets are up to 10 times less expensive than wired alternatives,” said Brent E. McAdams, Vice President, OEM & Strategic Initiatives at OleumTech. “Driven by substantial and measurable cost savings in engineering, installation, and logistics as well as dramatic improvements in the frequency and reliability of data, wireless sensor networks offer much faster startups, and accelerated profits.”
A wireless sensor network can be defined as a network of end nodes communicating information gathered from sensor locations through wireless links. Depending on the communications architecture, the data is either forwarded directly to a gateway or through multiple end nodes back to a gateway. The gateway is then connected to other devices or networks such as a wired or wireless Ethernet backbone to relay sensor information to a control system.
These networks are used to monitor a variety of conditions, covering all process control variables regardless of vertical market, including but not limited to pressure, flow, temperature, and level.
The oil and gas industry is one of the most active industries for the use of wireless sensor networks, usually located in remote areas with rough terrain, elevation challenges, and extreme ambient environmental demands. Wireless sensor networks are deployed to monitor, manage and control everything from tanks and compressors to generators, separators, and wellheads.
As operating costs have continued to rise while the price of oil experiences eight-year lows, wireless sensor networks offer advantages over the traditional wired technology where wired options are either too expensive or not even an option.
Wireless technology continues to make advances regarding applications, thus, eliminating the need for cables, allowing for cost-efficient network deployments. Wireless sensor networks may consist of many different types of sensors, covering a wide variety of applications consisting of pressure, temperature, flow, level or simply relaying a contact closure through a discrete transmitter.
Wireless sensor network applications most commonly cover monitoring of near real-time process control, safety, regulatory, and production performance.
“Energy harvesting” in the field is a key factor in wireless sensor network design simply because replacing batteries is not feasible; changing batteries for thousands of remotely deployed wireless sensor nodes could become an expensive logistical headache.
A variety of energy sources can be utilised to power wireless sensor end nodes. Solar, mechanical, and thermal energy are the primary sources. Given these options, harnessing solar energy is the most used and sophisticated energy harvesting technique. The frequency of transmissions drives power consumption. For individual condition monitoring applications such as monitoring tank level, latency in duty cycle is less important. However, reliability remains vital.
“Driven by the growing demand for advanced technology solutions to enhance productivity, efficiency, and profitability, all industrial sectors are harnessing the power of wireless sensor networks,” McAdams said. “Innovation is driven by data that enables operators to improve processes, reduce costs, enhance efficiency, make better decisions, and understand their customers’ unique requirements.”
未經允許,不得轉載本站任何文章: