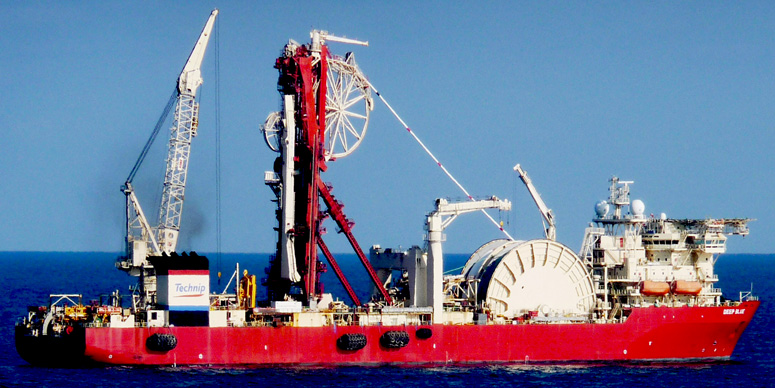
由于海上維修作業損失的生產時間,相當于每天數百萬美元的收入損失。為了避免出現這種狀況,研究出了對于管線的“實時”修復技術,即不需要任何停機時間的修復作業,這對于運營商來說是頗具吸引力的一個選擇,并且由于其自身相當高的靈活性和運營支出效率,該技術常常得到運營商的偏愛。然而,該操作在技術上卻具有一定的挑戰性。
在設計時海底管線的壽命一般為20年以上,但一些不可預知的損壞往往使他們達不到設計的最佳壽命。海底油氣管道的損壞可能發生在安裝或者操作過程中。2015年3月公布的海底管道及海上立管泄漏修復報告(PARLOC)中,提出了從2001年至2012年這12年間,發生在英國大陸架(UKCS)海底管道和海上立管的泄漏修復事件。在PARLOC報告中提到的183件泄露事件,有160件發生在操作過程中。據PARLOC報告稱,由于缺少匿名數據,無法獲得所有泄漏事件的完整描述。這些統計信息在世界其它地方可能不盡相同,但盡管如此,它還是突出了海上設備完整性的重要性,以及在發生管道泄漏時采取最新修復技術的必要性。
在操作過程中,管道損壞可能由管道內外部腐蝕、氫致應力裂紋(HISC)和環境因素造成的,例如與海底管道損壞相關的不穩定的海底條件或地震,以及第三方的影響,如錨和其它掉落的物體。損壞的風險由諸多因素共同決定,但一些典型的因素包括管道設計、環境條件以及人類在附近的活動強度。如果海底管道修復作業涉及到生產平臺隔離甲板部分,那么其他后勤方面的問題也同樣適用。
管道的損壞程度由輕微到嚴重變形或斷裂不等,其損壞的程度同時決定了在修復管道時所需要采取的方案。由于生產時間損失將對運營成本產生影響,因此對于發生大面積損壞的管道,修復工作通常僅限于利用帶壓開孔和旁路技術來切割和更換。對于大多數只是發生局部損壞的管道,諸如管道外部或內部腐蝕、局部范圍機械性損傷(例如凹痕,皺褶,變形或環焊縫缺陷),那些對生產時間影響很小或沒有影響的修復方法是可行的。這些修復方法被統稱為“實時”修復。
多數海底管線修復技術都會涉及到一些借助機械手段或者焊接聯接管線的配件,例如聯軸器、鉗夾、T型分支連接等。在管道修復過程中,隔離塞用于防止內部流體和海水填充管道排空的空間。再考慮一些后勤作業,海底管道修復作業具有一定的挑戰性并且成本頗高。通常,大多數的淺水管道修復(挪威海域水深180米/591英尺)一直由潛水員進行。在更深的水域,管道修復必須通過遠程控制技術進行。如果想獲得掌握這些技術和設備資質,則需要深入了解管道設計參數和具備豐富的操作經驗。迄今為止,關于深水和超深水管道修復方法仍具有很低的可選擇性。
過去的幾十年里,DNV GL集團在一些管道維修項目中一直擔任著獨立技術顧問,目標是使得“實時”管道修復不影響安全性和完整性。該公司已經開發了許多實用修復程序以及一系列“實時”修復方案。這些方案包括在管道中阻塞并注入堵漏材料對管道夾具進行修理,并對泄漏管線、注入堵漏材料的套管、管道三通用于氣體容器的裂縫套管和支座進行焊接修理。
DNV GL集團負責170項世界主要的海上標準和推薦規程(RPS)的修訂,目前,該集團正在通過快速聯合工業項目(JIP)更新其海底管道修復的一項主要RPS,即DNV-RP-F113。 RP作為參考,廣泛用于海底管道和接口的維修/修改的配件質量鑒定中。該參考指南包含這些配件和系統的設計、制造、安裝和操作方面。然而,RP最新版本公布于八年前,從那時起多項新技術都得到了發展。該新JIP旨在從管道維修設備和工具的主供應商和操作人員那里獲取最新最佳方法、經驗和專業知識,同時將海底管道維修標準和程序規范化,成為國際公認的標準。
在海底管道方面,RP的最新版本將與海洋標準的最新版本(即DNV-OS-F101)進行統一。并且將繼續擴大到能夠進行修復作業的范圍,包括外包管和內襯管的修復、管道表面的恢復、損害評估,既定管道損傷緩解和修復的方法進行選擇以及對管道維修作業生命周期的管理。
新版本還將對安全(包括甲板和陸地部分)和與阻礙海底管線維修的有關理論提供指導,并會對管道鋪設后的橢圓度和修復作業后的測試需求提供進一步的幫助。
其他改進后的設計和資格指南與管道隔離塞、酸性環境、高溫/高壓(HT/HP)管道修復、彈性密封件的壽命性能以及涂層去除工具對管道表面影響的驗收標準等內容有關。它還將在高壓焊接、對服役管道進行焊接爆裂極限檢查以及像去除縱向焊縫等安裝方面用于更新準則和驗收標準。
Loss of production time due to repair operations offshore can equate to millions of dollars per day in lost revenue. As a result, pipeline “live” repair, i.e. repair operations without any downtime, is an attractive option for operators, and is often preferred since it yields considerable flexibility and is highly opex-efficient. It is however, technically challenging.
Offshore pipelines are designed to last for more than 20 years, but damage can prevent them from reaching their optimal design life. Damage to oil and gas pipelines can occur during installation or during the operational stages. The Pipeline and Riser Loss of Containment (PARLOC) report published in March 2015 presents loss of containment incidents that occurred on pipelines and risers on the UK continental shelf (UKCS) during the 12-year period 2001 to 2012. The PARLOC report mentions 183 loss of containment incidents of which 160 happened during operation. According to PARLOC, full descriptions of all incidents are not available due to missing reported anonymous data. These statistics differ in other parts of the world, but nevertheless highlight the importance of offshore asset integrity, and the need to access the latest repair technology to respond when required.
During operation, damage can be caused by internal and external corrosion, hydrogen-induced stress cracking (HISC), environmental factors such as unstable seabed conditions or seismic related damage, and third-party impacts such as anchors and other dropped objects. The risk of damage depends on many factors, but typically includes the design of the pipeline, the environmental conditions, and the intensity of adjacent human activities. Additional logistical challenges also apply if the offshore repair operations involve isolating topsides on a production platform.
The extent of possible damage can vary from insignificant to a fully buckled or parted pipeline, and governs the repair preparedness strategy. For extensive damage of large sections of the pipeline, repair options are usually limited to cut and replacement using hot tap and bypass technology with substantial opex implications due to lost production time. For most local damage, such as external or internal corrosion and mechanical damage on a local scale (i.e. dents, wrinkles, buckles or girth weld defects), repair methods that involve minimal or no lost production time can be viable. These repair methods are collectively referred to as “live” repair.
Most subsea pipeline repair technologies involve fittings that can be connected to the pipeline via mechanical means, such as couplings, clamps, T-branch connections, or by welding. Isolation plugs are used to limit emptying volume of internal fluid and sea water filling of the pipeline during the repair. Offshore repairs can also be challenging and costly in terms of logistics. Most shallow-water repairs (down to 180 m/591 ft water depth in Norwegian waters) have historically been performed by divers. In deeper waters, pipeline repairs have to be conducted via remotely controlled technologies. Qualification of such technologies and equipment requires in-depth knowledge of the pipeline design parameters and operational experience. To date, there are very few options for deep and ultra-deepwater pipeline repair.
DNV GL has served as an independent technical advisor on several pipeline repair projects in the past few decades, to enable “live” pipeline repair without compromising on safety and integrity. The company has developed a number of practical repair procedures and a range of “live” repair solutions. These include plugging and grouted repair clamps for pipelines, and in-service welding of split-sleeves and stand-off sleeves with internal gas containment for repairs on leaking lines, grouted sleeves, and tees for pipelines.
Responsible for 170 world leading offshore standards and recommended practices (RPs), DNV GL is currently updating one of its leading RPs for offshore pipeline repair – DNV-RP-F113 – through a fasttrack joint industry project (JIP). The RP is widely referenced for the qualification of fittings and systems used for pipeline subsea repair and/or modifications and tie-ins. The guidelines include aspects relating to the design, manufacture, installation, and operation of such fittings and systems. However, the latest version of this RP was published eight years ago and a number of new technologies have been developed since then. This new JIP aims to capture the latest best practices, experiences, and expertise from the main providers and operators of pipeline repair equipment and tools, and to formalize pipeline subsea repair criteria and procedures into an internationally recognized standard.
The new edition of the RP will be harmonized with the latest revision of the Offshore Standard, DNV-OS-F101, on subsea pipelines, and will extend coverage to repair of clad and lined pipe, surface pipeline recovery, damage assessment, including root cause assessments, inspection methods, criticality assessment, selection of mitigations and repair methods for given damage levels, and lifecycle management of pipeline repair operations.
The new edition will also provide more guidelines on the safety (including topside and landfall) and barrier philosophy related to offshore pipeline repairs, and will provide further assistance on considerations for post-lay ovality of the pipe, and test requirements after the repair operation.
Other improved design and qualification guidelines will relate to pipeline isolation plugs; sour service; high temperature/high pressure (HT/HP) pipeline repair; the lifetime performance of elastomeric seals; and acceptance criteria for possible effects on the pipeline surface from coating removal tools. It will also address updated guidelines and acceptance criteria on hyperbaric welding, burst capacity check for welding on in-service pipelines, and installation aspects such as longitudinal seam weld removal.
未經允許,不得轉載本站任何文章: